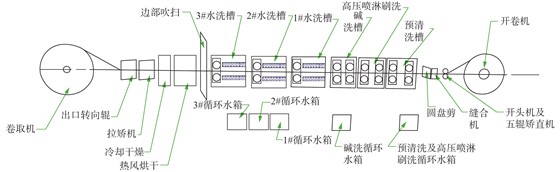
我国的铝工业发展虽然起步晚,但随着近些年大规模推进基础设施建设,以及工业进程的飞速发展,使得我国的铝加工行业也在朝向着高精尖的方向不断迈进。目前,铝合金板材广泛应用于航空航天、轨道交通、汽车以及电子产品等诸多领域。随着产品的应用范围不断的扩大,用户对于铝合金板材的表面质量的要求也日益提高,铝加工行业的竞争也日趋激烈。铝合金板材经过轧制、拉伸以及冲压等工序后,板材表面往往会存在轧制油等润滑油的污染,如果不及时清洗去除油污,可能会在后续的工序中产生深褐色油斑,从而严重影响铝板的产品外观,甚至导致用户退货的情况发生。因此在目前完整的清洗拉矫机组生产线的基础上,如何更好地利用现有设备以及更大程度地提高设备的清洗能力,使带材表面质量达到用户的要求显得尤为重要[1-2]。
本文对现阶段天津忠旺铝业有限公司的2350 mm铝合金板材清洗拉矫机组的清洗段设备和清洗工艺进行生产观察、实验对比,然后对设备及工艺方案进行优化改进,获取更好的清洗效果从而提高带材的表面质量,同时优化清洗段的系统稳定性。
1. 铝合金板材清洗技术现状分析
1.1 2350 mm清洗段主要设备及工作原理
2350 mm清洗拉矫机组清洗段主要包括预清洗槽、预清洗及高压水喷淋循环水箱、高压喷淋刷洗槽、碱洗槽、碱洗循环水箱、碱液配比系统、1#、2#、3#水漂洗槽、1#、2#、3#水洗循环水箱、边部吹扫、热风烘干和冷风干燥等。其生产过程示意图如图1所示。
2350清洗拉矫机组主要有重卷、切边、清洗、矫直四大功能,其工作方式为带材通过上卷小车从鞍座上输送入开卷机,带材经开头机及五辊矫直机后经入口夹送辊送入缝合机,与上一卷带材尾部进行缝合后自动穿带,然后经过切边后进入清洗系统。首先进入的是预清洗槽,水经过离心泵从预清洗循环水箱进入预清洗槽,通过喷淋杆上均布的扇形喷嘴进行常压水预清洗,然后经过预清洗1#及2#挤干辊挤干带材表面水分后进入高压喷淋刷洗槽,高压喷淋刷洗系统利用高压往复泵将水加压后送入高压喷淋刷洗槽内进行高压冲洗,刷洗槽内同时设有具备传动的上、下刷辊,刷辊的旋转方向与带材运行前进的方向相反,作相对反向运动,从而达到清洗运动带材的目的。经过高压喷淋刷洗然后进入碱洗水槽,碱液由计量泵打入碱洗循环水箱后,通过碱液配比形成合适的清洗浓度,从而对碱洗水槽内板带材进行碱洗,最后依次进入1#、2#和3#漂洗水槽,对带材表面的残余碱液进行冲洗。经过三个漂洗水槽末端的挤干辊,将带材表面的水分挤干后出水箱,经过边部吹扫装置对表面的残存水膜进行吹干后进入热风炉进行彻底烘干,再通过冷风对其进行冷却干燥处理避免其发生氧化。最后通过拉矫机进行板形矫正后经出口转向辊进入卷取机卷成整齐的铝卷进入下一道生产工序。
1.2 目前的清洗工艺
铝带材在经过冷轧等过程后残留的轧制油以及附着在油污上的铝粉等杂质严重影响板材表面质量,不能满足下游产品厂家和客户对于铝板表面清洁度的要求。铝加工行业现行的常用除油方法主要为高温碱法化学去油以及有机溶剂去油[3]。目前清洗机组采用的是先进行预清洗加高压喷淋刷洗去除带材表面的大颗粒铝屑以及附着在轧制油上的铝灰粉等杂质;然后进入碱洗槽中,利用碱液自动配比系统,根据测量碱洗循环回路中的电导率数值以及实际清洗效果来调整碱液配比浓度进行碱洗;最后进入三个水漂洗槽依次进行循环漂洗。
而清洗段目前采用的工艺是预清洗、高压喷淋刷洗、碱洗以及漂洗的全部喷淋杆喷嘴打开,这样容易导致由于流量增大而喷射压力减小,板材出现部分清洗不干净,残留铝灰泥及油印。同时边部积水增多易使得板材运行出清洗段时边部仍然带水较多,如图2所示。边部吹扫加烘干不能完全彻底地对板面进行干燥处理,影响板面质量,并且循环水回流的速度较慢时,水容易从溢流槽中溢出,影响生产线的整洁美观。当带材表面的带油及铝灰比较严重时,往往出现洗不干净需要二次冲洗的情况,这样也无形中增加了生产成本[4-5]。
2. 清洗技术改进措施
2.1 对预清洗及碱洗段的喷嘴数量进行改进
带材的最大宽度是2350 mm,而预清洗箱及碱洗箱中喷淋杆边缘的两个喷嘴的位置宽度是2420 mm。预清洗箱中原有喷淋杆有16根,其中8根喷淋杆上均布12个扇形喷嘴,8根喷淋杆上均布11个扇形喷嘴,因此将预清洗原有边缘2个喷嘴拆卸下来,共拆除32个喷嘴,同时用堵头进行密封封堵以免压力泄露。碱洗箱原有喷淋杆28根,其中14根喷淋杆上均布12个扇形喷嘴,14根均布11个扇形喷嘴,同样将边缘的2个喷嘴拆下,共拆除56个喷嘴,同样进行堵头密封。在线的喷嘴数量减少88个后,预清洗循环以及碱洗循环水流量相对减小,压力相对增大,使得带材表面可以清洗的更为干净,拆下边缘位置喷嘴,不影响正常板材清洗的同时也减少了带材边缘积水的情况,使得带材离开清洗段进入烘干及干燥段时板面水分相对较少。
清洗段末端的三个漂洗水槽中的喷淋杆在带材板面的上、下分布,喷嘴分别朝向板面向下、向上,与板面成90°分布。这样清洗的积水不容易从板面流下进入循环水箱,同时板面的积水容易从1#水洗槽被运行中的带材带入2#和3#水洗槽中,导致2#和3#漂洗循环水箱的水量过大而时常溢出,而1#漂洗水循环箱的水量不断减少,系统会判断自动补水,增加了生产线水量的消耗。
将靠近水槽连接处挤干辊位置的两组喷淋杆朝向进行更改,将1#、2#和3#水洗槽的1组、2组喷淋杆改向与机组运行方向相反方向45°(图3),不仅可以减少带材将循环水带进下一个水洗槽的情况,而且同时节约生产线的耗水成本。
2.2 清洗工艺的改进
2.2.1 高压往复式活塞泵的循环特性
生产线清洗段高压喷淋刷洗循环系统采用的往复式活塞泵[6],其耐压性高,转速范围宽,传输效率较离心泵高,活塞泵的工况调节主要是改变压力P和流量Q。调节压力主要通过调节排出阀的开度大小来实现进入水槽的循环水压头的改变;而流量的调节需要通过改变电机的转速。
生产线工作介质是循环水,由于清洗后循环水中杂质成分较多,调节排出阀则不好控制实际压力的大小,容易使得高压循环管路振动加剧,活塞泵的水流脉冲过大导致板材运行系统不稳定,或者过小导致泵的扬程不足,无法实现高压冲洗。因此需要调节电机转速匹配一个合适的压力进行高压冲洗。
对高压往复泵进行电机转速及压力的对比实验,结果如表1所示。
从表1中可以看出,当高压往复泵电机转速设定为70%时,管路压力达到6.87 MPa,这时循环管路振动情况适中,板材受流量脉冲的影响较小,同时带材系统运行平稳,清洗效果尚佳。
2.2.2 清洗段循环泵特性调节
生产线清洗段除高压喷淋刷洗采用的是高压往复泵外,预清洗、碱洗以及三个漂洗循环均采用卧式单机离心泵,且均采用“一用一备”的方式并联入循环系统。其中预清洗以及漂洗采用的是不可调速电机,碱洗采用的是可调速电机。
离心泵也同往复泵一样,具有运行工况的特性曲线,泵在恒定转速下,对应于泵的每一个流量Q,也相应对应着一个确定的扬程H、效率η、功率n和必需的汽蚀余量。
泵运行过程中,为使泵运行在高效区或者稳定区,需要对泵的工况点进行调节,而泵的实际工况点的改变途径包括改变泵的特性曲线和装置特性曲线调节。通过对预清洗循环泵和水漂洗循环泵进行恒转速工况实验,通过改变装置来调节特性曲线,对比泵的特性。预清洗槽设置有8个入口手动球阀,分别关闭1个开启7个;关闭2个开启6个,以此类推进行循环泵特性实验。根据预清洗水箱循环泵出口以及经过换热器后管路的压力表读数来进行分析(表2)。
从表2实验结果可以看出,当泵的转速恒定的情况下,关闭阀门减小流量的同时,1#泵及2#泵的出口压力从0.48 MPa上升到0.55 MPa,经过换热器后压力由0.43 MPa上升至0.53 MPa。
从表3实验结果可以看出,调节泵的电机转速,阀门的开关数量不变时,14对喷淋杆全部打开,压力变化较为平缓,而当阀门总开关数量为7对打开,7对关闭时,压力急剧增长,而当电机转速超过额定转速的90%后,对于循环水压力的增长几乎没有太大的影响。
据此结果可知,在生产线的清洗段中,对于预清洗以及漂洗段,在来料板材表面的铝灰及油污较多时,可以采用关闭若干组手动球阀,使得循环水的流量减小,而循环泵的转速恒定时,其压力呈现平稳增大的过程。而对于碱洗段,可以适当地增加电机转速,使循环泵的特性曲线向右上方移动,减小节流损失,保持高效率,且变速范围不宜过大,最低转速不宜小于额定转速的50%,否则泵本身的效率明显下降,耗电经济性差。
3. 结束语
设备改进方案以及工艺优化已在天津忠旺冷轧一厂2350 mm铝板带清洗拉矫机组的调试阶段完成,现清洗工艺稳定。在设备改造和工艺改进之后,铝板表面清洁度显著提高,铝灰残留以及轧制油斑减少,成品率提升,使得机组清洗效果以及机组运行有了较大改善,同时生产效率也得到提高,节能减耗成果显著,为企业创造出较为可观的经济效益,也对未来铝合金清洗生产线的技术研究开发具有积极意义。
来源--金属世界