刘海淙1,李湘萍2
(1.厦门航空有限公司飞机维修工程部,厦门361006;
2.中国民航大学中欧航空工程师学院,天津300300)
摘 要:建立了基于三维数字图像相关(3DGDIC)的非接触光学测试系统,对2A12铝合金弹性
常数进行了测试,在此基础上分析了DIC子区和步长的大小对材料弹性常数测试结果的影响,并
探讨了2A12铝合金在拉伸载荷作用下的变形演化规律.结果表明:3组2A12铝合金试样测得的
弹性模量和泊松比分别为66.32,67.51,63.08GPa和0.333,0.336,0.347;改变子区大小将引起图
像噪音的变化,对测试结果的影响较改变步长的影响更为明显,步长则主要作用于DIC算法的运
行时间;2A12铝合金试样在整个拉伸过程中依次经过弹性变形、均匀塑性流动以及应变局部化三
个阶段后发生断裂.
关键词:2A12铝合金;弹性常数;数字图像相关;子区;步长;灵敏度分析
中图分类号:O348.1;TG146.2 文献标志码:A 文章编号:1001G4012(2018)08G0557G06
DigitalImageCorrelationTestMethodandItsParameterSensitivityAnalysisforElasticConstantsof2A12Aluminum Alloy
LIUHaicong1,LIXiangping2
(1.AircraftMaintenanceEngineeringDepartment,XiamenAirlines,Xiamen361006,China;
2.SinoGEuropeanInstituteofAviationEngineering,CivilAviationUniversityofChina,Tianjin300300,China)
Abstract:NonGcontactopticalmeasurementsystem basedonthreeGdimensionaldigitalimagecorrelation
(3DGDIC)wasestablishedtotesttheelasticconstantsof2A12aluminumalloy.TheeffectsofdifferentsizesofDIC
parameters,i.e.subsetsizeandstepsize,ontheelasticconstanttestresultsofthematerialwereinvestigated,and
thedeformationevolutionlawof2A12aluminumalloyundertheactionoftensileloadwasalsodiscussed.The
resultsshowthattheelasticmodulusandPoissonratioofthreegroupsof2A12aluminumalloyspecimenswere
66.32,67.51,63.08GPaand0.333,0.336,0.347,respectively.Changingthesubsetsizecausedthechangeof
imagenoise,subsetsizehadmoreinfluenceonthetestresultscomparedtostepsize,andstepsizemainlycontrolled
thecomputationaltimeofDICalgorithm.The2A12aluminumalloyspecimenfracturedafterthreestagesofelastic
deformation,uniformplasticflowandstrainlocalization.
Keywords:2A12 aluminum alloy;elasticconstant;digitalimagecorrelation;subsetsize;stepsize;sensitivityanalysis
数字图像相关(DigitalImage Correlation,DIC)技术是应用计算机视觉技术的一种图像测量方法,它将物体表面随机分布的散斑作为变形信息的载体,可用于测量材料或结构件受外载荷作用下的全场位移和应变分布[1].由于该方法拥有试验光路简单、精度高、普适性强、受环境影响小等优点,已应用于结构变形破坏检测[2]、生物工程[3]、航空航天[4]等许多工程技术领域.其中,将DIC技术用于材料宏、微观力学性能的测试是其应用的一个重要方向[5G6].白晓虹[7]运用二维数字图像相关(TwoGDimensionalDIC,2DGDIC)技术,以DP590双相钢和304不锈钢为试验材料,测得各自的塑性应变比r 值以及全场r 值分布;胡斌等人[8]通过在圆柱体橡胶试样单轴压缩试验中采集变形图像,得到小应变范围内橡胶的应力G应变曲线,计算出材料的弹性模量.ZHU 等人[9]利用三维数字图像相(ThreeDimensionalDIC,3DGDIC)测试系统并搭载电子万能试验机,研究了低碳钢棒材在拉伸载荷作用下的全场塑性变形演化过程,并通过3DGDIC 还原的试样三维形貌获得了瞬时净截面积,进而绘制出了材料的真应力G真应变曲线.
2A12铝合金具有高强度、高韧性和可进行热处理强化等优良性能,成为了航空工业中应用最广泛的铝合金之一[10G11].目前,对该材料拉伸弹性常数的测试研究多数采用接触式的测试方法,例如采用引伸计和电阻式应变片,获得标距段的平均工程应变或某些离散位置的点应变.传统测试手段具有以下两点不足:①应变片一般只满足单点、单向测量,难以追踪试样在整个拉伸过程中的变形情况,以及材料在非均匀变化出现后的应变局部化现象;②引伸计有易打滑、
易损伤试件以及自重和夹持力会引起试件附加变形等缺点[12],给材料应变测量带来一定的误差.笔者利用先进的DIC 光学测试系统和分析软件,对2A12铝合金在单轴拉伸载荷作用下的全场纵向应变和横向应变进行了试验测量,通过拟合相关曲线获得材料的弹性模量及泊松比;在此基础上,围绕DIC算法运行过程所涉及的两个重要参数子区和步长,对其不同尺寸对测试结果的影响开展了灵敏度分析,为其合理取值提供参考;最后利用DIC全场测量的优越性,对试样表面随拉伸过程的变形演化规律进行了探讨.
1 数字图像相关法及其关键参数
图1为利用3DGDIC技术测量试样表面三维位移的示意图.首先在左相机拍摄的参考图像中确定分析区域(AreaofInterest,AOI).由于单一像素点的灰度值不具有唯一性,通常不可能在变形图像中识别出与参考图像相同的单个像素点[13].因此,为了精确辨识测试点P(x0,y0,z0)的空间位置,软件建立了一个以该点为中心并包含(2M +1)×(2M +1)像素的正方形子区(Subset),通过相关性计算可追踪右相机参考图像中的对应子区.根据预先标定的相机内外部参数可获得P 点的三维坐标.同样地,在变形后左、右相机拍摄的数字图像中也可追踪出该图像子区的相应位置,从而确定变形后中心点的三维坐标P1(x1,y1,z1).二者坐标之差即为所求的三维位移(u,v,w ),其中u 和v 表示面内位移,w 表示离面位移.最后对位移场采用有限应变方程进行差分计算,求得物体表面相应的应变场,即横向应变εxx 、纵向应变εyy 以及剪切应变εxy
在数字图像匹配过程中,DIC技术采用空域迭代的非线性优化算法,如NewtonGRaphson算法和效率更高的GaussGNewton算法,结合高精度亚像素插值格式[14],求解相关函数中用来描述变形子区精确位置和形貌特征的位移向量及位移梯度.DIC技术是全场全过程追踪试样表面变形信息的光学测试方法.
当采集数量较多的变形图像时,如疲劳试验,图像匹配算法将重复运行上百万次,这就对DIC的运行效率提出了相当高的要求.为此,通过设定步长(Step)大小,人为控制子区相关性计算所间隔的像素点数量,可以在一定程度上缩短算法运行时间.由此可知,子区和步长的取值将直接影响DIC测试精度.
2 试样制备与试验方法
2.1 试样制备
T228.1-2010«金属材料拉伸试验第1部分:室温试验方法»确定如下:厚度为1 mm,总长度为160mm,平行段长度为80mm,宽度为12.5mm,形状为标准哑铃型.采用黑白哑光漆人工喷制黑白相间的随机散斑,作为DIC追踪试样表面变形的信息载体.
2.2 试验方法
试验装置包括Instron5982电子万能试验机,最大载荷为100kN,同时搭载2台像素分辨率为3248×4872pixel2的AVTProsilicaGE4900型相机,采用焦距为105mm 的RodenstockRodagon镜头,共同构成3DGDIC 光学变形测量系统.表1为相机通过圆点标靶标定后获得的内、外部参数.其中:相机光心位置和焦距长度的单位均为像素;角度α,β,γ 分别表示光轴的转角、相机夹角以及相机2相对相机1的水平倾角;Tx ,Ty ,Tz 是2台相机的
间隔距离,分别为-220.351,0.313,49.934mm,基线距离为225.936mm.由表1可知,2台相机基本被固定在同一水平面,相距225.936mm,夹角约为20°.
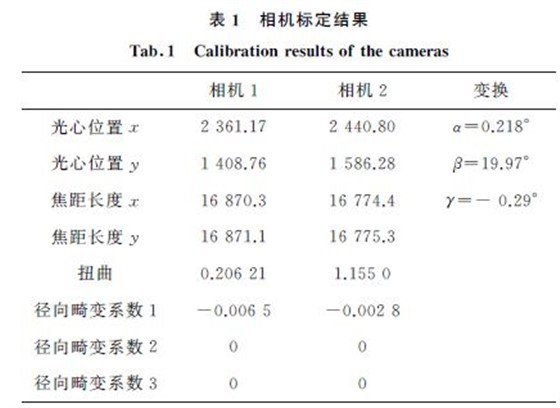
试样下端固定,上端沿机架竖直向上缓慢移动,并处在相机的视场中央,如图2 所示.试验开始时,2台相机同时开启,拍摄试样整个拉伸过程的数字图像,采集频率为0.5 帧??s-1.电子万能试验机按位移方式加载,速率为1mm??min-1,数据采样频率为1点??s-1,分别记录时间、位移、载荷和拉伸应力4 种信息.在分析软件中,首先划分DIC 计算的分析区域(图2),几何尺寸为12×70 mm2,对应分辨率为310 × 1 810 pixel2, 尺度因子λ =25.85pixel??mm-1.用于相关性计算的子区和步长初始大小设置为35×35pixel2 和7pixel.
图2 2A12铝合的3DGDIC位移测量示意图
Fig.2 Schematicdiagramof3DGDICdisplacementmeasurement
of2A12aluminumalloy
3 试验结果与讨论
3.1 2A12铝合金弹性常数测试
每个采样时刻下AOI纵向工程应变均值εDIC yy 和横向工程应变均值εxDxIC分别为
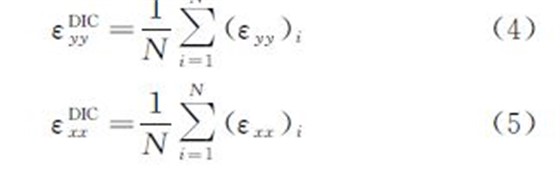
式中:N 表示DIC测试点数量,(εyy )i 和(εxx )i 分别表示第i 测试点的纵向工程应变和横向工程应变.
图3 2A12铝合金试样在拉伸应力下的工程应力G应变曲线
Fig.3 EngineeringstressGstraincurvesof2A12aluminumalloy
specimensundertensilestress
工程应力取自电子万能试验机,为瞬时载荷除以初始截面积.由此绘制试样在拉伸载荷作用下的工程应力G应变曲线,如图3所示.对材料弹性阶段进行线性拟合,相关系数用R2 表示,直线斜率即为材料的弹性模量E.由图3可见,2A12铝合金的工程应力G应变曲线主要分为两个部分,即应力迅速增加的弹性阶段和大范围塑性变形阶段,并且材料没有发生明显的屈服现象.试样的泊松比υ 为拟合横向应变G纵向应变曲
线所在直线的斜率,即
图4为2A12铝合金试样在拉伸应力下的横向
应变G纵向应变曲线.最终利用DIC技术测得3组2A12铝合金试样的弹性模量、泊松比、抗拉强度及断裂应变,见表2.由表2可知,3号试样的力学性能参数与另外两组试样的差别较大,其弹性模量较1号试样和2 号试样分别减小了3.24 GPa 和4.43GPa.可能是组成3号试样的合金成分含量与另外两个试样的不同,减弱了晶体结构的原子结合
力.1号试样和2号试样的平均弹性模量(66.92±0.84)GPa、平均泊松比0.335±0.002均与文献[15]给出的结果非常接近,表明该试验环境下DIC方法测得的应变结果是有效的.
图4 2A12铝合金试样在拉伸应力下的横向应变G纵向应变曲线
Fig.4 TransversalstrainGlongitudinalstraincurvesof2A12
aluminumalloyspecimensundertensilestres
以2号试样为例,其弹性应变范围在0~0.004,断裂应变为0.173,只占2.3%,说明材料经历的弹性阶段在试验开始后很快就结束了,而大范围的塑性变形直观地表明了2A12铝合金具有良好的延展性。
图6 步长尺寸对弹性模量和泊松比测试结果的影响
Fig.6 Influenceofstepsizeonthemeasurementresultsofa elasticmodulusandb Poissonratio
步长主要作用于局部应变的灵敏度,对于整体匹配过程的影响则可以忽略.此外,该值与DIC计算的数据点密度相关:随着步长的减小,密度随之增大,图像匹配算法的运行次数增加,计算时间也相应延长.因此,从计算效率的角度出发,步长取值不宜过小. 3.3 全场应变分析
图7 2A12铝合金全场纵向应变分布
Fig.7 Fullfiledlongitudinalstraindistributionof2A12aluminumalloy
充分利用DIC技术拥有全场、全过程追踪被测试样表面变形的独特优势,对2号试样从开始拉伸直至断裂过程中的力学行为进行分析,图7a)~j)表示不同时刻测量得到的纵向应变分布图.随着试验的进行,2号试样平行段宽度随之减小,其全场纵向应变分布开始出现不均匀性,相应的局部化现象发生.进一步观察可以发现,2号试样的塑性区最先开始于平行段下端,并且沿着材料的纵轴方向逐渐上下扩展.拉伸应力尚未达到材料的抗拉强度前,全场应变峰值相差较小,分别为0,0.023,0.025,0.027,0.030,0.033,见图7a)~f).当拉伸应力达到抗拉强度后,应变差值迅速增大,分别为0.039,0.049,0.062,0.145,同时新的应变不断在应变集中区(颈缩区)涌现而停止向外扩展,并最终在该区域发生断裂,见图7g)~j).图8为2号试样分别在颈缩区和全场范围的应变变化率对比.首先是弹性阶段(第Ⅰ阶段),应变率保持在较低的水平;当试验进行至t=45s时,应变率第一次增大,发生在材料弹性变形向塑性变形的过渡阶段,此后试样在单轴拉伸载荷下经历了很长一段时间的均匀塑性变形(第Ⅱ阶段),直到应变局部化现象发生;随后颈缩区的应变率迅速增大,而在全场范围内保持不变(第Ⅲ阶段).
4 结论
(1)应用DIC技术测得2A12铝合金平均弹性模量和泊松比分别为66.92GPa和0.335,该方法避免了引伸计对试样表面造成损伤及引起附加变形。
(3)试验研究了2A12铝合金在单轴拉伸载荷下全场应变的演化规律,试样经历短暂的弹性变形以及较长时间的塑性均匀流动后出现了应变局部化现象,沿材料纵轴方向上下扩展。
(文章来源:材料与测试网)