铝化物涂层改性Super304H 钢
在模拟锅炉煤灰/气环境中的腐蚀行为
李 琰1,2,鲁金涛1,杨 珍1,黄锦阳1,周永莉1,朱 明2
(1.西安热工研究院有限公司,国家能源清洁高效火力发电技术研究中心,西安 710032;
2.西安科技大学材料科学与工程学院,西安 710054)
摘 要:利用粉末包埋法在Super304H 钢表面制备了铝化物涂层,在模拟锅炉煤灰/气环境中对涂层改性前后的Super304H 钢和 HR3C钢分别进行了650,750℃腐蚀试验,对比分析了其腐蚀行为及腐蚀机制.结果表明:铝化物涂层主要由FeAl和Fe3Al相组成;在650℃腐蚀500h后,涂层改性前Super304H 钢表面氧化膜出现大面积剥落,而涂层改性后的钢表面则形成了均匀致密的Al2O3 膜;在750 ℃腐蚀时,涂层改性前Super304H 钢在腐蚀200h后其表面氧化层完全剥落,而涂层改性后的钢经500h腐蚀后,表面氧化膜剥落较改性前的轻,比650 ℃时的严重;铝化物涂层
提高了Super304H 钢的耐腐蚀性能,但高铬含量的 HR3C钢在650℃和750℃下均表现出更好的耐腐蚀性能.
关键词:煤灰/气环境;高温腐蚀;铝化物涂层;Super304H 钢
中图分类号:TG172 文献标志码:A 文章编号:1000G3738(2017)05G0089G06
0 引 言
随着超(超)临界发电技术的发展,锅炉的蒸汽温度和 压 力 不 断 提 高 (再 热 器 出 口 蒸 汽 温 度 高 达620 ℃,其壁温达到了670 ℃),这使得锅炉烟气侧材料的腐蚀问题日益突出,给机组的安全运行带来了极大的挑战.
目前,细晶强化的Super304H 钢仍是机组末级过/再热器的首选材料[1].据测算,管外壁温度达到640~680 ℃,才能使蒸汽参数达到620 ℃级超(超)临界二次机组的要求.因此,需要对 Super304H 钢在更高温度下的耐烟气腐蚀性能进行进一步的研究.目前,针对Super304H 钢在高温烟气侧腐蚀行为的研究报道较多[2G4].已有结果表明,Super304H钢的腐蚀过程受服役温度、烟气成分及煤灰组成等诸多因素影响,其中温度和烟气中的硫是最主要的影响因素[5].PETTERSSO 等[6]对18G8型不锈钢在不同温度下的腐蚀行为进行了研究,发现该不锈钢的腐蚀速率随温度的升高明显加快.NATESAN等[7]的研究亦证实了这一点,并指出腐蚀速率峰值出现在725 ℃左右,这与620 ℃二次再热机组烟气侧的温度相近,显然,在此温度下 Super304H 钢会发 生 严 重 腐 蚀.STEINGBRZOZOWSKA[8] 和ZENG[9]等通过改变服役环境中的硫含量后发现,随着烟气中硫含量的增加,合金的腐蚀进程显著加快.实际锅炉运行时的测试结果与之相符,燃烧低品质煤(高硫、高钠煤)会显著加快锅炉材料的腐蚀,导致早期失效[10].一些模拟煤灰/气环境中的腐蚀
研究结果表明,煤灰黏附在金属表面时会形成低熔点碱金属硫酸盐,在650 ℃及更高温度下这些碱金属盐呈熔融态,这加速了金属腐蚀[9].由此可见,在更高的服役温度及高硫烟气下,Super304H 钢的耐腐蚀性能较差,这限制了其进一步的应用.为满足更高等级超(超)临界机组运行要求,所用材料问题的解决思路主要有两种:一是用高强度和高耐蚀性的高温合金来替代现役奥氏体耐热钢,如Inconel740H 合金等[11G12];二是对现役管材涂敷高温防护涂层.由于前者成本过高且缺少服役运行数据支持,其应用受到了限制;后者则因具有成本低、易实施等特点得到了广泛应用.研究发现,涂敷
铝化物涂层的 NiGCrGW 高温合金具有良好的抗高温氧化性能[13],但其耐热腐蚀性能不佳[14G15],涂层与基体之间的元素扩散导致涂层退化严重.而铝硅、铝铬涂层可以很好地解决上述铝化物涂层的不足.王心 悦 等[16]研 究 发 现,经 铝 硅 共 渗 处 理 后,M951合金表面形成连续的θGAl2O3 膜,合金耐腐蚀性能得到了显著提高.而铝铬共渗涂层中因同时含有铝元素和铬元素,能大幅度提高 Super304H 钢的抗高温氧化和耐热腐蚀性能[17].在已有研究基础上,作者采用粉末包埋工艺在Super304H 钢表面制备了铝化物涂层,研究了涂层改性前后Super304H 钢在模拟锅炉煤灰/气环境中的腐蚀行为,同时以高铬含量(质量分数为25%)的HR3C钢为参比对象,从耐蚀元素含量的角度探讨了降低合金腐蚀速率的控制措施,为现役及下一代锅炉机组用材料的选择提供参考.
1 试样制备与试验方法
试 验 材 料 有Super304H钢 ,名 义 化 学 成 分 如表1所示;FeAl粉和 NH4Cl粉,粒径均为48mm,国药集团提供;以 HR3C钢作为耐腐蚀性能分析的参比对象,其名义化学成分见表1,该钢中铬元素含量较高,为高铬钢.
将Super304H 钢 加 工 成 尺 寸 为15mm×10mm×2mm 的试样,用1200# 砂纸打磨后,用酒精清洗、吹干.采用粉末包埋法在试样表面制备铝化物涂层.按照FeAl粉和 NH4Cl粉质量比为98∶2配制混合粉,将试样包埋在混合粉中,升温至950 ℃保温2h,随炉冷却,酒精清洗、吹干后待用.在模拟锅炉煤灰/气环境中进行腐蚀试验.将含2% (质 量 分 数,下 同)Na2SO4,2%K2SO4,6%Fe2O3,22%Al2O3 和29%CaSO4 的合成煤灰刷涂于涂层改性前后 Super304H 钢和 HR3C 钢试样表面,煤灰用量为40~50mg??cm-2,然后将试样用合金丝串起 悬 挂 于 管 式 炉 中 进 行 腐 蚀,试 验 装 置 如图1所示.管式炉中通入由1.5%(体积分数,下同)SO2,3.5%O2,5%H2O,10%CO2 和 80%N2 混合组成的模拟煤气,流量为100mL??min-1,催化剂为铂网,腐蚀试验温度分别为650,750 ℃.反应后的尾气用饱和氢氧化钠溶液吸收后排出.在试验过程中,每隔一段时间取出试样并清洗干净,称取质量,观察后重新涂覆煤灰继续试验.
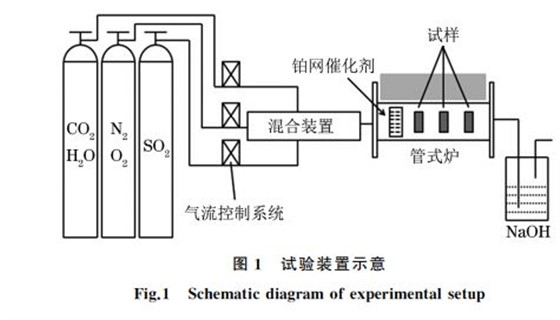
用精度为0.01mg电子天平称取试样质量,计算腐 蚀 质 量 变 化;用 HitachiGS4800 型 扫 描 电 镜(SEM)观察铝化物涂层、腐蚀层表面和截面形貌,
并用 附 带 的 能 谱 仪 (EDS)分 析 其 元 素 组 成;利 用ShimazduG7000SX 型 X 射线衍射仪(XRD)分析腐蚀产物的物相组成.为便于观察腐蚀层形貌,部分腐蚀试样进行了喷金及化学镀镍处理.
2 试验结果与讨论
2.1 铝化物涂层的显微组织
由图2可知:采用粉末包埋法制备的铝化物涂层分内外两层,厚度分别为40,15μm;涂层主要由FeAl和 Fe3Al相组成.由 EDS点成分分析可知,外层 和 内 层 中 铝 元 素 的 平 均 质 量 分 数 分 别 为33.15%和12.43%.
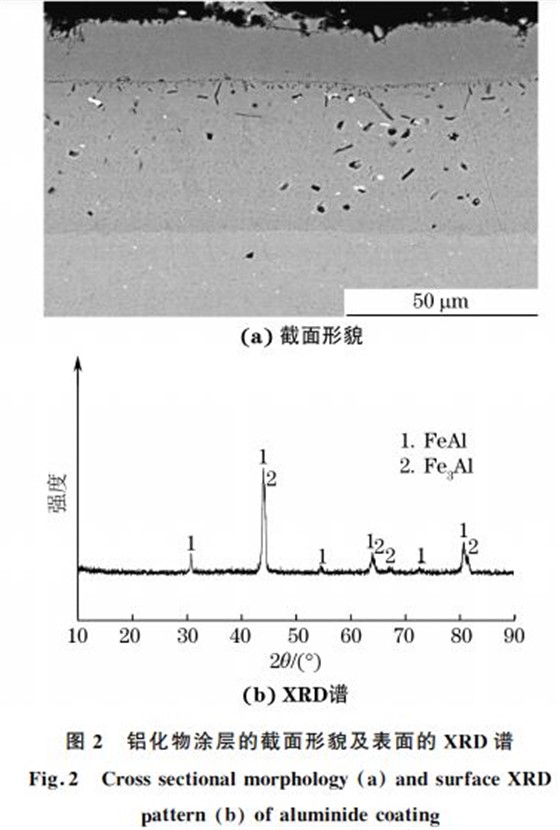
2.2 腐蚀质量变化
由图3可知:在650℃下,涂层改性前Super304H钢在腐蚀初期的质量增加较快,50h达到峰值,之后连续大幅下降,直至出现严重的腐蚀质量损失;涂层改性 后 Super304H 钢 的 腐 蚀 质 量 增 加 缓 慢,在50h后 出 现 轻 微 的 下 降,腐 蚀 质 量 损 失 较 小.在750℃下,涂层改性前Super304H 钢在腐蚀20h后 出 现 严 重 的 腐 蚀 质 量 损 失;涂 层 改 性 后Super304H 钢在腐蚀前100h内出现明显的腐蚀质量增加,200h后质量增加缓慢下降.而 HR3C 钢在两种温度下均表现出良好的耐腐蚀性能,腐蚀质量增加变化较小.
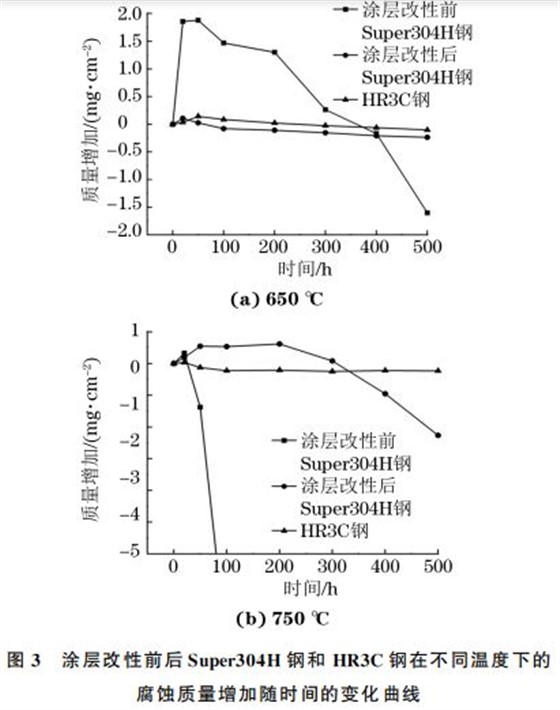
2.3 腐蚀产物形貌
由图4可知:在650 ℃腐蚀500h后,涂层改性前 Super304H 钢 发 生 了 明 显 的 腐 蚀,表 面 氧 化膜大面积 剥 落,且 出 现 明 显 的 分 层、断 层 现 象,腐蚀层较 厚 (约 为 40μm);涂 层 改 性 后 Super304H钢表面氧化膜相对平整,厚度均匀,未发生明显的腐蚀剥落,腐蚀层中出现细小的针状腐蚀产物,涂层与基体界面清晰可见;HR3C钢表面形成了一层
致密、完整、很薄(厚度约为4μm)的氧化膜,氧化物颗粒细小.
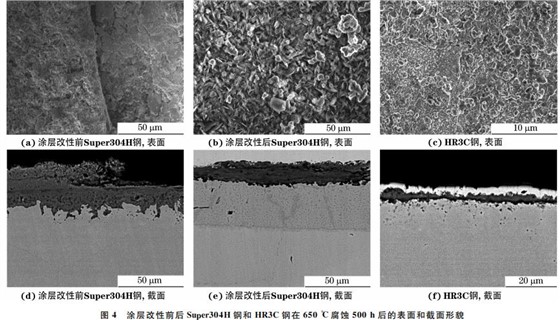
由图5可知:在750 ℃腐蚀200h后,涂层改性前Super304H 钢的表面氧化膜已完全脱落,基体内部发现大量腐蚀产物;涂层改性后Super304H 钢在腐蚀500h后表面氧化膜的剥落相对较少,但局部区域出现溶解腐蚀现象,与650 ℃腐蚀500h的相比,其表面针状腐蚀产物的尺寸增大;铝化物涂层与基体的界面均模糊不清,说明该涂层的耐腐蚀作用已逐渐减弱甚至消失.HR3C钢表面氧化膜出现腐蚀破裂现象,氧化膜变得疏松多孔,与650 ℃腐蚀500h的相比,其氧化膜厚度明显增大(约为12μm).
2.4 腐蚀产物组成
由图6 可 知:在 650 ℃ 腐 蚀 后,涂 层 改 性 前Super304H 钢表面腐蚀产物主要为 Fe2O3 和少量FeCr2O4;涂层改性后 Super304H 钢表面腐蚀产物以 Al2O3 为 主. 在 750 ℃ 腐 蚀 后,涂 层 改 性 前Super304H 钢表面除了上述腐蚀产物外,还出现少量硫化物;涂层改性后Super304H 钢表面则生成了Fe2O3、Al2O3 和 FeAl2O4 等多种腐蚀产物.在两种温度下,HR3C 钢表面的腐蚀产物基本不变,以Fe2O3 和 Cr2O3 为主,并存在少量 FeCr2O4.
2.5 分析与讨论
在模拟煤灰/气腐蚀环境中,钢腐蚀是由低熔点碱金属 硫 酸 盐 及 氧 化/硫 化 交 互 加 速 作 用 而 导 致的[18G20],主要化学反应如下:
2SO2+O2 ??????2SO3 (1)
3K2SO4+Fe2O3+3SO3 →2K3Fe(SO4)3 (2)
3Na2SO4+Fe2O3+3SO3 →2Na3Fe(SO4)3 (3)
Na3Fe(SO4)3 和 K3Fe(SO4)3 的熔点较低,分别为624 ℃和618 ℃.在试验温度下,这两种盐为熔融态,可与涂层改性前Super304H 钢表面的由氧和铬、铁所形成的氧化膜发生溶解反应.此时,环境中的硫、SO2/SO3 等腐蚀性介质通过膜中的缺陷向膜内扩散并与钢中的合金元素生成网状结构的硫化物(FeS、CrS等),这为元素外扩散及腐蚀介质的内扩散提供了快速通道,加快了该钢的腐蚀进程.随着氧的内扩散,部分内硫化物被氧化释放出活性硫,硫会继续向内扩散形成新的硫化物.此过程循环进行,因此在腐蚀层/基体界面处始终有硫化物的存在.通常情况下,硫化物阳离子空位浓度大,原子在硫化物 中 具 有 更 高 的 扩 散 速 率,且 其 分 子 体 积(PVB)较大,会增大膜层的内应力,导致氧化膜开裂或剥落[21].涂层改性前 Super304H 钢的表面膜层以铁的氧化物为主.由于 Fe2O3 的稳定性较差,易发生硫酸盐化,因此随着腐蚀的进行,Fe2O3 膜逐渐被溶解失去保护性,导致该钢腐蚀较严重.与650℃相比,涂层改性前Super304H 钢在750 ℃腐蚀20h后出现严重的腐蚀质量损失,至200h,表面氧化层已完全脱落,表现出极差的耐腐蚀性能,显然,温度的升高加快了膜层的溶解腐蚀进程.涂层改性后 Super304H 钢的表面形成了连续致密、黏附性较强且稳定的 Al2O3 保护膜.该膜层阻碍了腐蚀性气体和熔盐向钢基体内的扩散[22],且由于 Al2O3 膜具有一定的自修复 能 力,一 旦 被 破坏,铝元素向表面迁移又会形成新的 Al2O3 膜,因此铝化物涂层改性后Super304H 钢的耐煤灰/气腐蚀性能得到了大幅度提高.虽然涂层改性后 Super304H 钢的耐腐蚀性能得到了显著提升,但与高铬含量的 HR3C 钢相比其耐蚀性能仍旧较差.这主要有几个方面的原因:一是涂层与基体中元素的互扩散会造成涂层中的铝元素损失严重,导致该涂层失效[23G24];二是 Al2O3 膜层在熔盐中的稳定性较差,易发生硫酸盐化出现溶解现象而导致涂层失效[25];三是由于向外扩散的铁元素一方面被氧化形成 Fe2O3,另一方面与铝反应形成新的 Fe3Al层,随着腐蚀时间的延长,Fe2O3 和FeAl2O4 逐渐增多,贯穿整个涂层,形成快速扩散通道,使涂层失去了对基体元素的阻挡作用,导致了涂层失效[14G15].从试验结果看,Super304H 和 HR3C钢虽同为奥氏体耐热钢,但在高温煤灰/气中的耐腐蚀性能差异较大.在试验周期内,HR3C 钢表现出了较佳 的 耐 腐 蚀 性 能,这 与 其 高 铬 含 量 有 关[5].
Cr2O3 的形核和生长较快,通过选择性氧化在较短时间内就能在 HR3C 钢表面形成一层连续致密的Cr2O3 保护膜.Cr2O3 膜在熔盐中稳定性较好,不易发生溶解腐蚀,大幅提高了 HR3C 钢的耐腐蚀性能[26].综上可见,铝 化 物 涂 层 改 性 虽 可 显 著 提 高Super304H 不锈钢在煤灰/气中的耐腐蚀性能,但HR3C钢由于具有较高质量分数的铬使得其耐腐蚀性更加优异.
3 结 论
(1)采用粉末包埋法在 Super304H 钢表面制备了铝化物涂层,该涂层分内外两层,厚度分别为40,15μm,该涂层主要由 FeAl和 Fe3Al相组成.
(2)在650 ℃模拟煤灰/气中腐蚀后,铝化物涂层改性前 Super304H 钢的腐蚀质量增加随腐蚀时间的延长先增大,当腐蚀时间达到50h后大幅度下降,腐蚀500h后表面氧化膜大面积剥落,表面腐蚀产物主 要 为 Fe2O3 和 少 量 FeCr2O4;涂 层 改 性 后Super304H 钢的腐蚀质量增加明显比涂层改性前的低,且变化较平缓,这主要是因为该钢表面形成了
均匀致密的 Al2O3 膜,提高了其耐腐蚀性能.
(3)在750 ℃模拟煤灰/气中腐蚀后,涂层改性前Super304H 钢在腐蚀20h后出现严重的腐蚀质量损失,腐蚀200h后其表面氧化膜完全剥落;涂层改性后Super304H 钢经500h腐蚀后,表面氧化膜剥落相对于涂层改性前钢的少,但比650 ℃下腐蚀的严重,且表面针状腐蚀产物尺寸增大,腐蚀产物主要为 Fe2O3、Al2O3 和 FeAl2O4 等.
(4)与铝化物涂层改性 Super304H 钢相比,高铬含量的 HR3C 钢在650 ℃和750 ℃下均表现出较好的耐腐蚀性能,铬元素是提高此钢耐腐蚀性能的关键.
晶界处富集铜元素的θ′(Al2Cu)相溶解,向 T1 相转变,大量析出的强化相 T1 能有效阻碍位错运动,从而形成弥散强化.接头伸长率的下降与热处理过程中接头焊缝晶粒的长大、晶界析出相等导致位错在晶界处塞积有关.
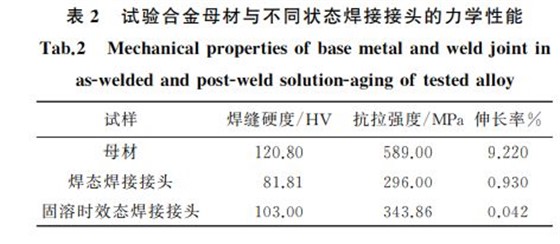
3 结 论
(1)在试验条件下,2195GT8 铝锂合金激光焊接接头获得熔透且背部无明显下塌焊缝的热输入Q约为160J??mm-1,在P=6kW,v=2.2m??min-1时试验合金可以获得成形良好,内部无气孔、裂纹等缺陷的焊接接头.
(2)焊态下焊缝熔合线区的组织为细小的等轴晶,焊缝中心为等轴晶和粗大的树枝晶;焊缝区的组织软化严重,为整个焊接接头的薄弱区;与母材相比,焊缝的硬度下降了32.3%,焊接接头的抗拉强度下降了约49%,断裂形貌为沿晶脆性断裂.
(3)经过固溶时效处理后,合金焊缝的组织更加均匀,晶粒长大,同时晶界及晶内析出许多弥散且较均匀分布的 T1(Al2CuLi)相,焊缝的硬度明显升高,比固溶时效处理前的提高了25.6%,抗拉强度则提高了13.7%.
文章来源:材料与测试网