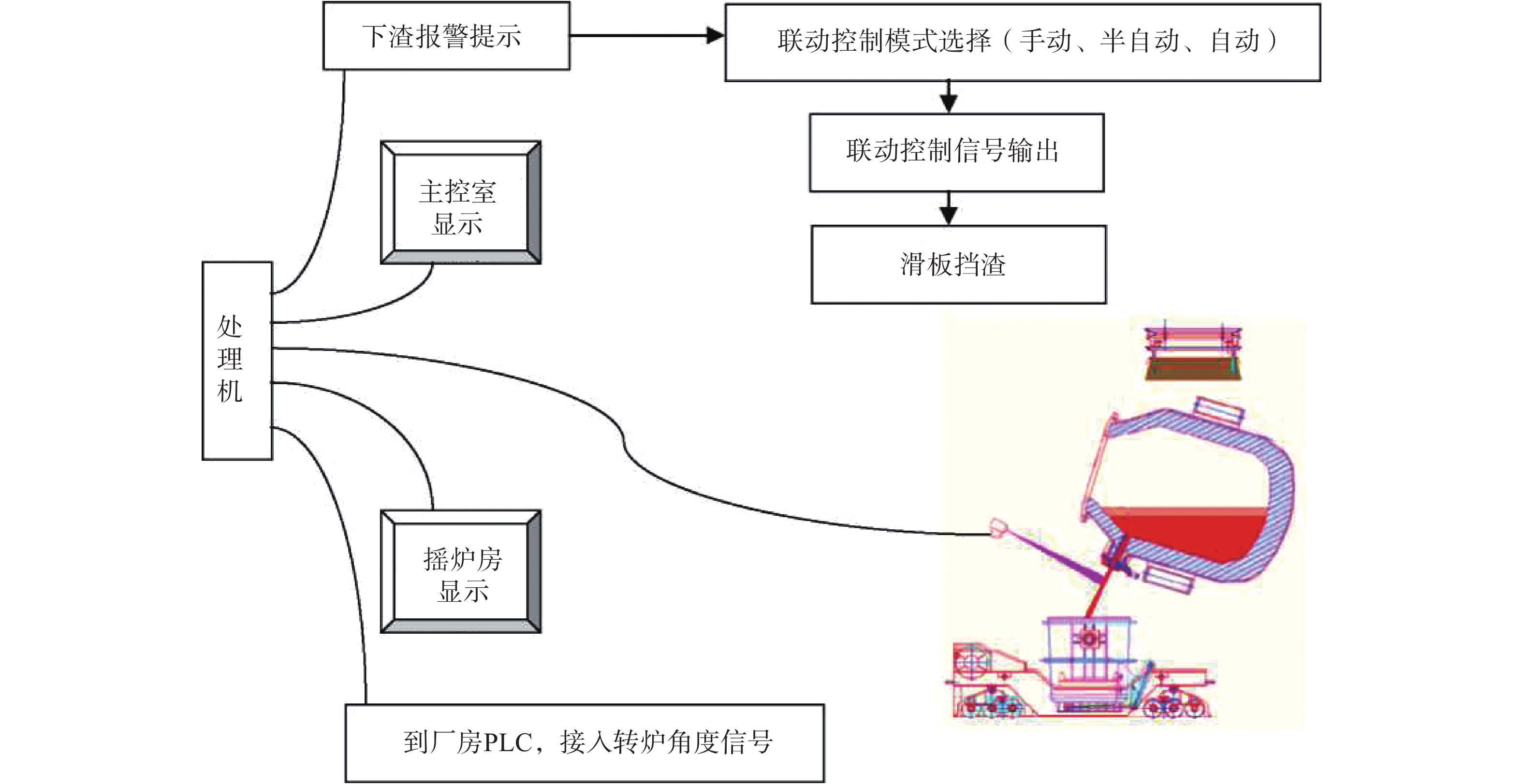
分享:转炉出钢滑板挡渣+挡渣标技术的实践与应用
转炉炼钢是氧化法炼钢,冶炼后期在钢水降碳的同时会存在大量富余氧,而且由于脱磷的需要使得炉渣氧化性比较强,进入下道工序会造成脱氧成本的增加及脱氧产物影响钢水的洁净度。随着汽车板的生产、品种钢的开发、市场质量的需求不断提高都对钢水质量提出了更高的要求。最大限度控制转炉下渣量是一个转炉炼钢世界性难题,围绕挡渣技术国内先后普遍采用过挡渣球、挡渣标(或挡渣锥)、滑板挡渣等挡渣技术。近几年,随着滑板挡渣技术的成熟和稳定,各钢厂开始陆续采用滑板挡渣技术进行转炉出钢过程的挡渣操作,虽耐材成本有一定的增加,但挡渣效率非常高,故障率很低,挡渣效果良好,逐步被各钢厂接受。但是采用滑板挡渣技术后出钢时由于地磁引力的作用在出钢后期钢水面会出现涡流效应,同时为了保证挡渣效果,在钢渣分配比20%~30%进行挡渣操作,会有少量的钢水滞留在炉内,造成一定程度的钢铁料损失。
1. 滑板挡渣设施的挡渣原理
1.1 滑板挡渣设施的挡渣基本原理
滑板挡渣过程示意图见图1,用于挡渣的滑板安装在转炉出钢口的外部,挡渣效果取决于设备的稳定性。经过三年多的实践验证表明,滑板挡渣设备稳定,挡渣效果良好。出钢后期通过红外下渣检测系统检测到钢渣混合比20%~30%,发出滑板关闭信号;由液压系统驱动滑板在1 s内将滑板关闭;在转炉本体转动力矩提升过程中,倾动抱闸未打开,转炉无法转动的2~3 s时间内,将剩余钢渣挡在炉内。滑板挡渣技术的优点是挡渣效果好,渣厚控制水平≤40 mm,设备基本无故障,挡渣的稳定性好,渣厚控制水平不波动,生产秩序稳定。滑板挡渣技术的缺点:由于地磁引力作用钢水面在出钢后期会出现中间低边缘高的涡流现象,在出钢后期炉内钢水较少时部分炉渣会混入钢水中进入钢包中;红外检测系统检测到下渣信息后,向挡渣系统发出信号,滑板挡渣设施关闭滑板,会有少量钢水滞留在炉内,造成不必要的钢铁料损失;挡渣耐材费用相对挡渣标(或挡渣锥)偏高。
1.2 下渣检测系统钢中渣比例设定对剩钢及渣厚的影响
由表1可见:钢中渣比例设定低于20%时,渣厚控制水平小于30 mm,转炉出钢后会出现明显剩钢现象,普通冶炼不推荐采用,但冶炼特殊品种可采用;钢中渣比例设定为30%时,渣厚控制水平30~40 mm之间,通过溅渣观察到有少量钢花存在,证明有少量剩钢,倒渣时,因渣偏粘看不到,不好标定,推荐采用,这时的渣厚水平对质量和成本相对性价比较高;钢中渣比例设定为40%时,渣厚控制水平40~70 mm,出完钢炉内无钢水,但由于钢包渣层偏厚,影响精炼工序的钢水处理,不推荐采用。
钢中渣比例/% | 剩钢量/kg | 最大渣厚/mm |
10 | 500~800 | 20 |
20 | 300~500 | 30 |
30 | 溅渣有钢花 | 40 |
40 | 无钢水 | 70 |
2. 挡渣标(或挡渣锥)的挡渣基本原理
挡渣标(或挡渣锥)的挡渣示意图见图2。挡渣标(或挡渣锥)挡渣原理:转炉出钢后期由挡渣车夹持挡渣标(或挡渣锥)进入炉内,下倾后投放挡渣标(或挡渣锥);投放结束后,升大臂,然后将挡渣车向炉后开出,挡渣标(或挡渣锥)投放在转炉的内部钢渣界面上。挡渣效果取决于投放设备的稳定性、挡渣标(或挡渣锥)的质量和密度的选择、转炉出钢口的里口形状,且转炉出钢口的里口形状在出钢口更换周期的前、中、后期不一样,对挡渣效果影响也比较大。挡渣标(或挡渣锥)挡渣技术的优点是挡渣成本相对较低。挡渣标(或挡渣锥)挡渣技术的缺点:挡渣有效率在80%~90%左右,稳定性差;渣厚控制水平40~200 mm,波动较大;易出现挡渣标(或挡渣锥)熔化或标、杆分离、投标时机不恰当等问题;一旦挡渣出问题,转炉倾动系统由于防止跑炉,2~3 s内转炉倾动系统力矩提升过程中抱闸不能打开,会造成此期间转炉下渣量较大,导致钢包带渣量较大,对后序生产影响较大,严重时,可能导致铸机断浇。
3. 滑板挡渣+挡渣标(挡渣锥)组合式挡渣的实践与应用
结合滑板挡渣+挡渣标(挡渣锥)两种挡渣方式的优缺点,将两种挡渣技术组合在一起使用,既保证了原来挡渣标(或挡渣锥)的优点,对于挡渣效果好的炉次,经滑板挡渣二次挡渣后,渣厚水平再次降低;而挡渣效果欠缺的炉次,则可依靠滑板挡渣系统挡渣,对最终的挡渣效果不会产生影响。两种挡渣技术的组合虽造成了挡渣标(或挡渣锥)成本的增加,但由于挡渣标(或挡渣锥)的挡渣成功率在80%~90%,总体性价比还是合适的。组合式挡渣技术的使用起到了两种挡渣技术上优势互补和扬长避短,既减少了转炉出钢后期炉渣的下渣量又达到了降低生产成本的目的,可以提高钢水质量,有利于品种钢的生产,有较高的推广价值。
3.1 渣厚的影响
从表2中看出,采用滑板挡渣+挡渣标(或挡渣锥)组合方式较单采用滑板挡渣方式渣厚减少7 mm。经过两种挡渣技术的组合使用,对转炉生产出钢过程没有影响,挡渣效果优于单种挡渣技术,转炉下渣量进一步减少,利于品种钢的生产和产品质量的提升。
挡渣方式 | 渣厚/mm |
滑板挡渣 | 38 |
滑板挡渣+挡渣标(或挡渣锥) | 31 |
3.2 原因分析
图3为滑板挡渣炉次后期出钢钢流的红外线图,从图中看出,钢流饱满,但相应钢流较大。图4为挡渣标(或挡渣锥)投入到炉内后钢流红外线图,从图中看出,由于挡渣标(或挡渣锥)在出钢过程后期已经投入到出钢口里口部位(见图2),破坏钢水由于引力作用产生的涡流效应,钢水面较原来平稳,避免了提前下渣现象,挡渣标(或挡渣锥)在出钢口里口部位占用部分出钢的通道,使得钢水流变小,出钢结束滑板挡渣使用时,同样的响应时间里,下渣量会减少,同时,由于钢水流变小滑板关闭时,钢水对滑板迎钢面的冲击损伤减少,可以提高滑板的使用寿命,降低滑板耐材成本,达到了转炉出钢过程采用滑板挡渣+挡渣标(或挡渣锥)组合技术的目的,优势互补,扬长避短,既减少了出钢过程下渣量,又降低了生产成本,同时可提高钢水质量。
4. 效益分析
4.1 耐材成本
耐材成本基本不增加。虽然增加了挡渣标的耐材成本费用,但由于滑板挡渣挡渣时钢流和渣流变小,滑板的侵蚀下降,可以提高滑板的使用寿命,降低滑板的耐材费用,二者成本基本互相低消。滑板挡渣的使用情况见图5,从滑板的侵蚀情况看,还可以增加滑板的使用次数。
4.2 钢铁料成本
由于减少了涡流效应,转炉出钢后炉内基本无钢水,经标定钢铁料收得率提高0.5 kg/t左右,吨钢效益1.0元以上。
5. 结束语
滑板挡渣+挡渣标(或挡渣锥)组合挡渣方式生产可行,相比滑板挡渣方式渣厚减少7 mm,有利于高级别品种钢的冶炼,减少钢水的夹杂物;破坏了涡流效应,使得转炉出钢后炉内基本无钢水,吨钢效益在1.0元以上。
来源--金属世界