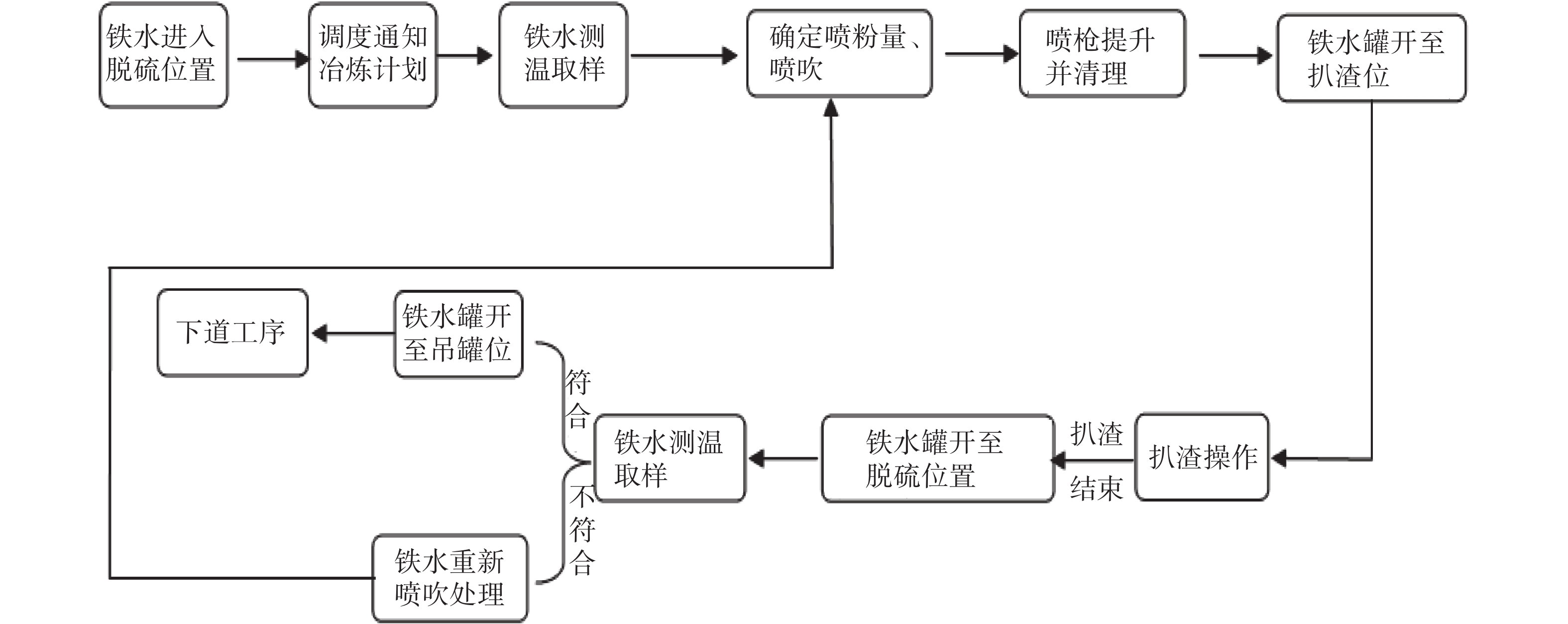
分享:低硫硅钢硫控制工艺优化
摘要:
本钢生产低硫硅钢时对硫含量的要求极低,因而常出现硫含量较高使得硅钢产品不合格的现象,导致低硫硅钢的炼成率较低。本文跟踪生产数据进行分析得出,当S入站质量分数<0.032%时,通过增加镁粉喷吹量,控制尽可能低的转炉上一炉倒炉硫、钢包上一炉钢包硫,同时控制好废钢、原辅料尽可能为低硫含量等,能够有效提高低硫硅钢炼成率。
低硫硅钢生产的控制难点在于低硫硅钢为超低碳钢,必须经过RH处理,且它对硫含量(质量分数)的要求极低,要求w(S)≤0.004%,按照炉产180 t计算,进入钢水的硫含量大于7.2 kg时就会造成成分不合格,故低硫硅钢对硫的控制关键集中在原料预处理和转炉阶段,如何控制好预处理和转炉阶段的脱硫是本文研究的重点。
本钢的铁水脱硫工艺流程如图1。CaO+Mg复合喷吹主要设备参见文献[1]。
炉产180 t的低硫硅钢中如进入钢水的硫含量大于7.2 kg时就会造成成分不合,而硫的来源主要在铁水、废钢、炼钢用的原辅料及盛装钢水的转炉、钢包所含带的渣中。具体原辅料含硫量及进硫量见表1,镁粉复合喷吹的脱硫极限质量分数为0.0015%,如原辅料进硫量(质量分数)>0.0025%,便会导致成品不合格(由于铁水硫含量非常低,故此处忽略了炼钢的脱硫作用),因此除了控制工艺过程外,还应确保废钢、炼钢用的原辅料均为低硫含量或尽可能控制硫含量高的物料加入量,如用低硫含量的石灰石代替部分活性石灰冶炼等。
预处理过程中,以溶于铁水的[Mg]参与脱硫反应为主,生成MgS,该方式是复合喷吹脱硫的主要反应形式[2]。当镁单独存在时,脱硫反应主要按式(1)进行[3]:
式中,ΔGθ为吉布斯自由能,J/mol。
当有CaO存在时,MgS不稳定,会与CaO进一步反应,见式(2):
文献[1]中相关实验表明:流态化石灰基本上没有起到脱硫作用,复合喷吹法的脱硫产物主要是不稳定的MgS,未生成更稳定的CaS。
镁粉主脱硫反应步骤:
(1)镁粉溶解到铁水中形成[Mg],此期间镁粉的溶解扩散需要一定的时间。
(2)[Mg]与铁水中的[S]接触生成MgS。
(3)反应到一定程度,如想进一步降低铁水中[S],需要铁水中含有更高的[Mg],即在一定温度下[S]与[Mg]之积为常数,[S]降低则[Mg]升高反应才能进行,此期间一是需要喷吹更多的镁,二是需要一定的反应时间。
(4)当初始硫过高时,存在着渣硫间的分配平衡,达到动态平衡时,必须通过增大渣量及增加反应扩散时间才能进一步脱硫。
(5)镁粉脱硫的一大弊端是产生回硫,主要是因为:处理铁量大,铁水罐中动力学条件不足,罐中存在部分死区,这部分死区的硫含量仍为铁水初始硫含量;脱硫产物MgS需要形核长大之后上浮到渣中,如果反应时间不够,MgS来不及上浮到渣中,就会残留在铁水中,进入转炉造成回硫。因此,须有足够时间保证MgS尽可能都上浮到渣中,同时确保扒渣扒净,才能尽量降低回硫。
(1)铁水到站温度。温度对脱硫反应有不同的影响,一方面随着温度的升高Mg的溶解度降低,由于Mg脱硫反应是放热反应,因此温度的提高不利于脱硫。另一方面,温度的提高有利于脱硫反应的[Mg]在铁水中的扩散及脱硫产物的上浮排出,从生产数据分析可知:如想达到成品硫质量分数≤0.004%,铁水到站温度在1345~1365 ℃利于低硫控制。
(2)喷吹石灰量。经过实验研究发现喷吹石灰中的CaO不能起到脱硫的作用,但它可以稀释渣中(MgS)的含量,使脱硫反应利于向正向进行。从生产数据分析可知:喷吹石灰量越多,越利于成品S的控制,其中石灰量大于390 kg时,炼成率相对较高。
(3)喷吹镁粉量。脱硫反应反应到一定程度,如想进一步降低铁水中[S],需要铁水中含有更高的[Mg], [S]降低则[Mg]升高反应才能进行。从生产数据分析可知:镁粉喷吹量大于180 kg时,利于成品S的控制。
(4)转炉上一炉倒炉硫。转炉上一炉倒炉硫与残留在转炉中的渣中硫息息相关,呈正相关关系,是带入硫的一项关键因素。从生产数据分析可知:转炉上一炉倒炉硫质量分数小于0.007%,利于成品硫的控制。
(5)钢包上一炉钢包硫。转炉上一炉钢包硫与残留在钢包中的渣中硫呈正相关关系,是带入硫的另一项因素。从生产数据分析可知:转炉上一炉钢包硫质量分数小于0.006%,利于成品硫的控制。
(6)入站S。理论上分析:入站S越低,在喷吹量和镇静时间足够的前提下,相对来说,成品S易于控制。但从生产数据分析可看出:入站S质量分数在0.032%~0.045%时利于成品S的控制。
为了进一步寻找理论和实际的不同原因,选取入站S质量分数小于0.032%的炉次,根据喷吹量不同可以看出镁粉喷吹量≥180 kg的炉次成品S控制明显好于镁粉喷吹量<180 kg的炉次,说明产生上述情况的原因为喷吹镁粉量不够或镇静时间不够,MgS来不及上浮到渣中。但实际生产中对生产节奏有要求,只能通过多喷吹粉剂的方式利于MgS颗粒和其他固态粉剂簇集上浮,以利于成品硫的控制。
选取对低硫硅钢成品炼成率影响较大的可控数据S入站、镁粉喷吹量、转炉上一炉倒炉硫、钢包上一炉钢包硫进行改进,通过对比10炉冶炼合格及不合格数据可知:当S入站质量分数<0.032%时,对生产过程中的可控数据进行控制,通过增加镁粉喷吹量大于180 kg,控制尽可能低的转炉上一炉倒炉硫、钢包上一炉钢包硫,同时控制好废钢、原辅料等后续工序带入硫量,能够有效提高低硫硅钢炼成率。
冶炼低硫硅钢除控制工艺过程外,还应确保废钢、炼钢用的原辅料均为低硫含量或尽可能控制硫含量高的物料加入量。镁粉脱硫的一大弊端是产生回硫,应有足够时间确保脱硫产物MgS形核长大之后上浮到渣中,同时扒渣扒净,才能尽量降低回硫。S入站质量分数<0.032%时,增加镁粉喷吹量大于180 kg,控制尽可能低的转炉上一炉倒炉硫、钢包上一炉钢包硫,同时控制好废钢、原辅料等后续工序带入硫量,能够有效提高低硫硅钢炼成率。
1. 预处理脱硫工艺概况
2. 铁水硫控制分析
2.1 硫来源控制
物料
含硫量/%
添加量/t
进硫量/%
活性灰
0.050
5.5
0.0015
废钢
0.008
24.0
0.0011
石灰石
0.015
1.0
0.0001
菱镁石
0.025
2.0
0.0003
2.2 脱硫热力学分析
(1)
(2)
3. 铁水脱硫工艺分析
3.1 脱硫步骤
3.2 影响因素分析
4. 铁水脱硫工艺优化
5. 结束语