分享:镁/钛异种金属冷金属过渡焊接头应力场的有限元模拟
车洪艳1,刘国辉1,王 岑2,张海燕2,曹 睿2,陈剑虹2
(1.安泰科技股份有限公司,北京 100086;
2.兰州理工大学 有色金属先进加工与再利用省部共建国家重点实验室,兰州 730050)
摘 要:利用 ABAQUS有限元软件建立了镁/钛异种金属冷金属过渡焊接头的有限元模型,对焊接过程中接头的应力场进行了有限元模拟,分析了不同的焊接参数和约束条件下应力场的变化规律,并对模拟结果进行了试验验证.结果表明:随着焊接过程的进行,焊缝处的横向应力和纵向应力均由压应力向拉应力转变;在焊接接头完全冷却后,镁侧的最大横向残余拉应力值为88MPa,钛侧的为192MPa;在焊接接头完全冷却后,焊缝两侧的纵向残余拉应力峰值基本相等,大约为220MPa,钛侧的纵向残余压应力值较大,最大值为265MPa;采用耦合约束后,模拟得到的残余应力值与试验测试结果更接近.
关键词:镁/钛异种金属;冷金属过渡;焊接应力场;有限元模拟
中图分类号:TG457 文献标志码:A 文章编号:1000G3738(2017)05G0105G06
FiniteElementSimulationonStressFieldofMg/TiDissimilarMetal
JointWeldedbyColdMetalTransferMethod
CHEHongyan1,LIUGuohui1,WANGCen2,ZHANGHaiyan2,CAORui2,CHENJianhong
2
(1.AdvancedTechnology& MaterialsCo.,Ltd.,Beijing100086,China;2.StateKeyLaboratoryofAdvancedProcessing
andRecyclingofNonGferrousMetal,LanzhouUniversityofTechnology,Lanzhou730050,China)
Abstract:FiniteelementmodelofMg/TidissimilarmetaljointweldedbycoldmetaltransfermethodwasestablishedbyABAQUSfiniteelementsoftware,andstressfieldofjointsduringweldingprocesswassimulated.
Thevariationregularityofsimulatedstressfieldwithdifferentweldingparametersandconstraintswasstudiedandcomparedwithtestresultstofurtherconfirmtheaccuracyofthesimulationresults.Theresultsshowthatthetransverseandlongitudinalstressattheweldseamwerechangedfromcompressionstresstotensilestressduringtheweldingprocess.Aftertheweldingjointwascompletelycooled,themaximumtransverseresidualtensilestress
reached88MPaatthemagnesiumsheetand192MPaatthetitaniumsheet.Aftertheweldingjointwascompletelycooled,thepeakvalueofthelongitudinalresidualtensilestressatbothsidesallreachedabout220 MPa.Theresiduallongitudinalcompressionstressattitanium side was morethanthatoftheotherside,which hadamaximumof265MPa.Theresidualstressresultsbyfiniteelementsimulationwithcoupledconstrainedboundary
conditionwereclosetothatofthetestresults.
Keywords:Mg/Tidissimilarmetal;coldmetaltransfer;weldingstressfield;finiteelementsimulation
0 引 言
王涛 等[4] 采 用 冷 金 属 过 渡 (CMT)焊 接 技 术 对AZ31B镁合金和 TA2纯钛进行了搭接焊,发现存在接头变形大、焊接参数窗口窄、接头性能不稳定等问题.上述研究都说明镁/钛异种金属焊接时容易出现变形大、易开裂、焊接参数窗口窄等问题,而这些问题的出现和焊接过程中产生的残余应力有密切的关系.对于焊接残余应力的测试和模拟,国内外学者们已经做了大量的研究,目前残余应力的测试多采用 X 射线法与盲孔法,文献[5]结合有限元模拟和盲孔法对 LY12铝合金薄板焊接残余应力进行了较好的预测,文献[6]中也结合有限元模拟、盲孔法、X射线法等方法对焊接后接头上的应力分布进行了准确的分析.为了弄清楚镁/钛异种金属 CMT焊接过程中出现的焊接变形大、焊接参数窗口窄、接头性能不稳定等问题的原因,作者在试验[4]以及温度场模拟[7]的基础上,对镁/钛异种金属冷金属过渡焊接头的应力场进行了模拟,并通过试验对模拟结果进行了验证.
1 试验方法
试验选用尺寸均为200 mm×50 mm×1 mm的退火态 AZ31B镁合金和 TA2纯钛为待焊材料,选用直径为1.2mm 的 AZ61镁合金焊丝,采用奥地利 Fronius公司生产的 TPSG3200型系列数字化冷金属过渡(CMT)焊机进行钛板在上、镁合金板在下的搭接焊,搭接宽度为10 mm,如图1所示.焊接过程中,焊 丝 偏 移 镁 和 钛 的 搭 接 边 缘,偏 向 钛 板
1mm,以保证镁钛焊接接头具有较好的焊缝成形能力和力学性能[6].焊接过程中采用99.99%氩气保护,流量为15L??min-1,采用CMT 焊机自带的经过优化的焊接参数专家数据库—一元程序(送丝速度改变,焊接电压和焊接电流随之变化),送丝速度为11.5m??min-1,焊接速度为10 mm??s-1,焊接电流为110A,焊接电压为10.5V.焊接时间为20s,焊接后冷却至室温并开始测试残余应力.采用热电偶进行特征点热循环曲线的测量;根据 GB/T31310-
2014,运用 DH3815型静态电阻应变仪测量与记录钻孔处的应变,最后通过应变量计算出小孔处的残余应力分布.
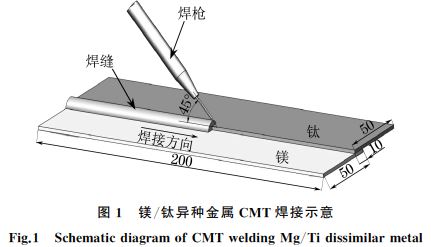
2 有限元模型的建立
通过 ABAQUS有限元软件建立一个三维(3D)有限元模型并运用 Fortran语言编写 DFLUX 子程序来实现热源的加载过程.根据 CMT 焊接镁/钛时的焊缝形貌,选用双椭球体热源模型[8].由于焊接是一个不均匀的加热过程,且焊缝及其热影响区的温度梯度变化较大,因此模型中采取不均匀的网格划分,在焊缝及近缝区采用较密的网格,而在远离焊缝区采用相对稀疏的网格[8],如图2所示.文献[7]中温度场求解时采用的网格类型是 DC3D8,单元个数为48000个,根据文献[7]中模拟得到的温度场采取顺序耦合的方法进行应力场求解.根据焊缝金属的填充过程,采用单元生死技术,即先将焊缝
金属移除,当焊接过程进行到每一单元时,再将每一单元逐一激活,并将材料参数恢复到之前设置的数值.在应力场求解过程中选用热G应力顺序耦合的方法,将第一次温度场计算所得到的节点温度作为预定义场来计算应力场,即只考虑温度对应力的影响,不考虑应力对温度的影响,将温度计算结果代入应力计算中.在加载边界条件时,提取模型中的几个作用点进行约束.对这些特征点在三个方向(x,y,z 轴)的自由度分别进行约束,保证在模拟的整
个过程中,不 出 现 刚 性 移 动.在 计 算 时 输 入 不 同温度下材 料 的 弹 性 模 量、泊 松 比、屈 服 强 度、线 膨胀系数等 参 数,如 图 3 和 图 4 所 示.在 焊 接 过 程中镁板会发生塑性变形,因此需要对 AZ31B镁合金在室温 时 的 塑 性 参 数 进 行 设 置.另 外,应 力 场分析时的网 格 与 温 度 场 分 析 时 的 一 样,所 以 在 应力计算过程 中 只 改 变 网 格 的 属 性,将 温 度 场 中 的热传导(heattransfer)改为应力(3DGstress).初始温度条件为25 ℃.通 过 上 述 模 型 计 算 和 分 析 焊缝填充过程 中 的 应 力 分 布,以 及 焊 后 的 残 余 应 力分布.对特 征 点 的 应 力 变 化 过 程 进 行 分 析,比 较不同边 界 条 件 情 况 下 的 残 余 应 力 分 布 和 变 形 情况,并将计算 所 得 到 的 结 果 与 试 验 测 试 结 果 进 行对比分析.
3 模拟结果与分析
3.1 应力分布云图
通过对焊板残余应力的模拟可以得到焊接接头的 Mises等效应力分布云图.图5(a),(b),(c)为焊接过程中的应力分布云图,图5(d),(e)为焊接结束后冷却过程的应力分布云图,图5(f)为冷却结束拆除焊接夹具后的残余应力分布云图.由图5(a)中可以看到,在焊接进行到4s时,热源靠近焊板,热源作用区域温度升高,熔池中心的金属熔化.在这个状态下热源作用区域的应力值几乎为零,在热源的前端钛板上应力达到212MPa,这是因为在加热过程中焊缝金属发生受热膨胀,对前端焊缝产生挤压,同时焊缝金属也受到周围金属对膨胀的抑制,从而产生该应力,在这个阶段中焊板的变形量很小.图5(b)为焊接进行到8s时的应力分布云图,应力分布与图5(a)的基本相同,但焊板产生了微小的变形.图5(c)为焊接进行到20s时的应力分布云图,此时已经凝固的焊缝金属温度开始降低,受到的拉应力值增大,起焊位置处的应力达到291MPa,同时,焊板也产生了比较明显的变形.图5(d)为焊接结束后冷却30s时的应力分布图,随着焊缝温度的降低,焊缝及其两侧的拉应力值继续增大,同时焊缝金属出现与前面相同的应力分布规律,最大应力值达到353 MPa,同时焊板的变形量也随之增加.图5(e)为焊接结束后冷却80s时的应力分布云图,焊板基本完成冷却,最大应力值出现的区域进一步扩大,焊接影响范围基本覆盖了整个钛板和镁板;焊板的变形已基本结束,与焊完冷却30s时的相比其变形量基本相同.图5(f)为焊接完成
并冷却87s拆除焊接夹具后的应力分布云图,夹具的拆除完全释放了焊接过程中夹具对焊板变形的抑
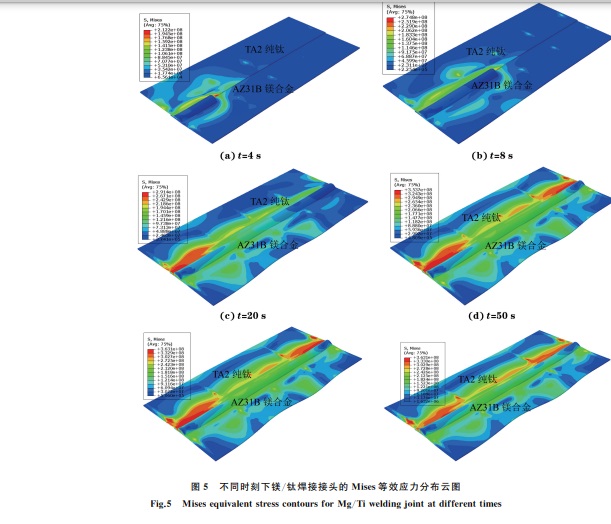
3.2 焊后残余应力的分布
由于焊接过程中焊板受到较大的横向收缩力与纵向收缩力,在焊后会产生较大的横向残余应力与纵向残余应力,这对焊板的变形有着很大的影响,因此需要对焊板的横向残余应力与纵向残余应力做进一步的分析.由图6可见:取整个焊板的中心,即距离起焊位置100mm 处作为应力分析的位置,也是焊接进行到整个过程的一半时的位置,该位置的应力分析具有一定的代表性.将此位置上垂直于焊缝方向的横向残余应力值与纵向残余应力值进行对比,分析残余应力随时间的变化,残余应力分析的路径如图6中节点所示.
从图7中可以看出,当焊接进行到10s时,热源移动到焊 板 的 中 心 位 置,该 位 置 焊 缝 处 的 应 力为压应力;随着焊接过程的进行,焊缝处的横向应力由压应力 转 变 为 拉 应 力,这 是 因 为 金 属 凝 固 过程中焊缝金 属 出 现 强 烈 的 收 缩 现 象,对 该 部 分 金属产生强烈 的 拉 伸 作 用,所 以 焊 缝 处 及 焊 缝 两 侧存在拉应力,而远离焊缝区域由于受到焊缝金属的挤压,产生的是压应力;焊接完成并冷却87s(完全冷却)时去除夹具后该位置钛侧的最大横向残余拉应力值为192MPa,而镁侧的则为88MPa.由图8可知:不同时刻该位置焊缝处的应力也是随着焊接过程的进行由压应力转变为拉应力;焊接进行到10s时热源经过此位置,熔池中心的应力值接近0MPa,焊缝周围为纵向压应力,钛板侧的压应力值比镁板侧的大,靠近钛板侧的压应力峰值为118MPa,靠近镁板侧的压应力峰值为42 MPa;接进行到16s时热源向前移动,焊缝金属开始凝固收缩,焊缝处出现150 MPa的拉应力;焊接完成并冷却87s(完全冷却)时去除夹具后该位置两侧焊缝处的纵向残余应力值基本相等,大约为220MPa,钛侧的残余压应力值较大,其最大值为265MPa,与镁板侧相比,钛侧还存在较大的压应力区域.
由于镁合金具有较大的热导率,镁/钛异种金属焊接时镁板侧的收缩量与收缩区域都比较大.同时,钛合金具有较大的弹性模量,因此钛侧的变形量比较小,但应力值却较大.
3.3 边界条件对残余应力的影响
横向残余应力有所增大,这是因为增大约束区域后,限制横向收缩的区域增大,导致这些区域的压应力值增大.图9(b)中的纵向残余应力值也发生了变化,尤其是约束部位与焊板边缘,采用耦合约束后钛板边缘的应力值接近于0,由于钛板没有发生塑性变形,在焊接过程中约束区域的增大导致焊板的纵向收缩受到抑制,因此纵向残余应力减小;而镁板边缘的纵向残余应力值增大是因为镁侧发生了塑性变形,故产生了更大的残余应力.
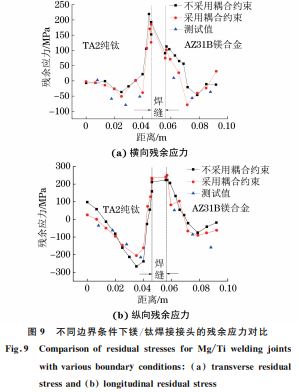
通过图9可以看出,采用耦合约束后焊板的残余应力模拟值与试验测试值更接近,整体变化趋势更吻合.
4 结 论
(1)通过有限元模拟可知,在焊接结束后焊板发生了明显的变形,焊板完全冷却并拆除夹具后,镁/钛焊接接头的最大残余应力出现在钛板侧热影响区,最大 Mises等效应力值为363MPa.
(2)随着焊接过程的进行,焊缝处的横向应力由压应力向拉应力转变,等待焊板完全冷却后,镁侧的最 大 横 向 残 余 拉 应 力 为 88 MPa,钛 侧 的 为192MPa;焊缝处的纵向应力的变化规律与横向应力的相同,焊缝两侧的残余拉应力峰值基本相等,大约为220MPa,钛侧的残余压应力值较大,其最大值为265MPa.
(3)模型采用耦合约束后,焊板的残余应力值与试验测试值更接近.