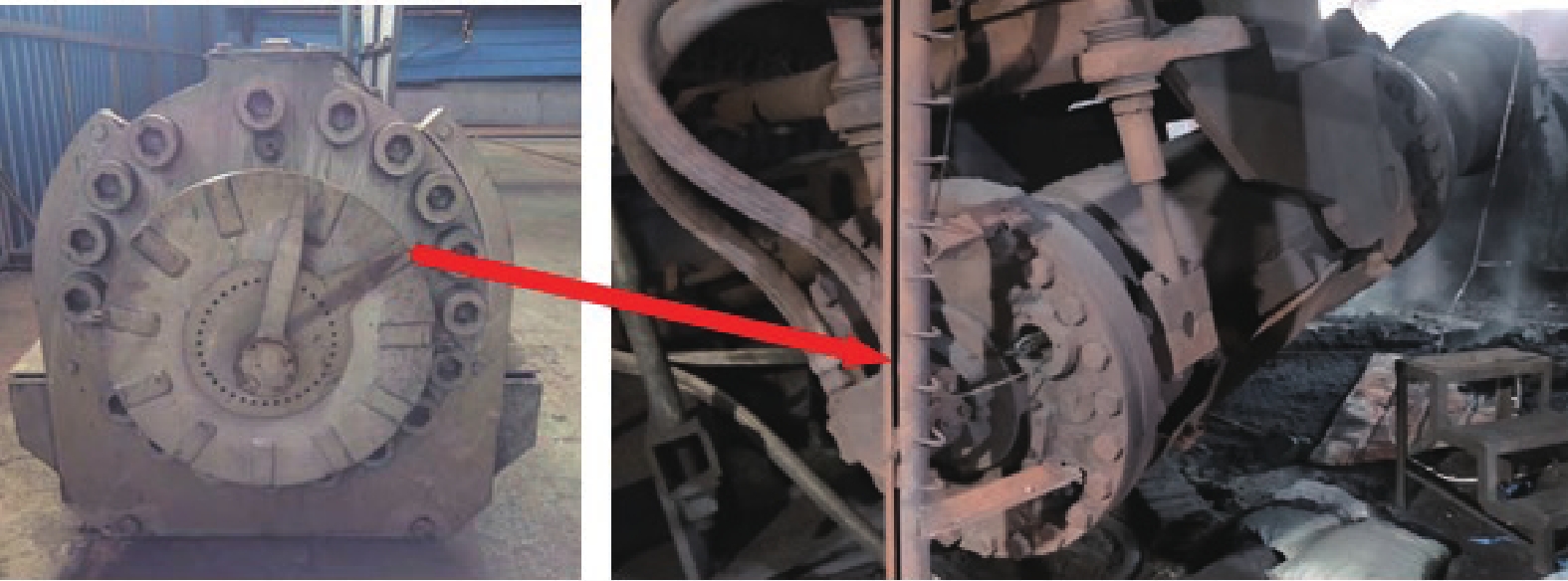
分享:液压泥炮打泥量精准控制研究与应用
目前,我国对高炉液压泥炮打泥量的研究集中在机械传动重锤式、钢绳传动式[1]、指针式等方面[2],但是,这些研究局限性在于只能估测打泥量,偏差大,无法准确控制铁口深度。然而,打泥量的多少直接影响高炉的稳定性,进而影响高炉稳产、高产。打泥量过大,会出现铁口深度过深、下次铁口难开、严重浪费炮泥;打泥量过少,造成铁口过浅、出铁时间短、严重影响炉缸的寿命[3]。国外文献分析打泥量时,大多只给出了相关结论,而没有说明具体的计算方法[4]。因此,研究液压泥炮打泥量精准控制很有必要。
1. 传统打泥量装置及精度分析
1.1 机械传动式打泥量装置
1.1.1 装置结构简介
图1为机械传动式打泥量装置。由图1可见,炮身尾部装有钢丝绳?滑轮?重锤式打泥行程指式器,用以显示打泥量的相对值,由于采用了动、静滑轮结构,故行程指示器指针的全行程为打泥活塞全行程。打泥液压缸活塞杆向前移动,带动钢丝绳传动,钢丝绳经过绳轮组成的滑轮组,带动指针旋转,指针转动角度的大小即为检测打泥量的多少。它是通过传动件的位移量来估测打泥量,估值偏差大,无法准确控制铁口深度。打泥量行程指示,检测的只是打泥液压缸活塞杆产生的位移,而不是液压泥炮实际射入铁口炮泥的量。
1.1.2 性能参数
液压泥炮采用机械指针式打泥量装置设计,其动作原理是由两个往复式活塞液压缸完成旋转、压炮、炮身倾斜、打泥等各种动作。为了使炮口在压炮状态保持向下倾斜10°±5°,且炮身在离开出铁口反向旋转时又不致碰到铁沟沟帮,液压泥炮旋转轴是倾斜的。直径8 mm钢丝绳穿过液压泥炮尾部端盖,由3组滑轮导向,把直线运动变为圆周运动,表盘分为12格,每格代表打泥量0.025 m3,液压泥炮旋转角度为114°±5°,打泥时间为75 s,其主要技术性能参数如表1所示。
泥缸容积/m3 | 泥缸直径/mm | 活塞推力/kN | 打泥速度/(m/s) | 炮口直径/mm |
0.3 | 480 | 5600 | 0.3 | 150 |
打泥活塞压力/MPa | 打泥液压缸最高压力/MPa | 打泥液压缸直径/mm | 打泥液压缸最大行程/mm | 液压炮旋转时间/s |
31 | 28 | 250 | 1650 | 10~15 |
1.2 打泥量精度低原因分析
1.2.1 人为操作原因
由于炉前操作者技能、经验和视力不一致,以及对铁口状况掌握程度不一致,每名操作者观察表针的角度不同,读数各不相同,每次凭操作者个人经验判断进行打泥操作,结果造成打泥量过大或过少。操作原因是造成铁口深度不合格的主要原因,危害极大。
1.2.2 现场原因
出铁后炉前堵铁口作业在液压泥炮操作室,通过远距离观察现场液压泥炮上安装的打泥行程指示,由于铁口周围烟尘、灰尘、粉尘大,视线差、看不清,造成读数偏差太大,可操作性差,铁口深度的控制主要靠操作人员的经验来判断。现场原因不可避免,虽然不是主要原因,但是危害较大。
1.2.3 其它特殊原因
液压泥炮堵铁口过程中,遇到炉况失常造成铁口喷吹,裸露的钢丝绳挂渣铁卡住或者被渣铁烧断;有时遇到铁沟潮湿放炮,崩坏表盘、烧毁表针,此时操作者无任何参照物,只能凭借打泥时间来判断打泥量多少。这种情况一旦发生,操作者为了避免堵不上铁口多打泥,会出现铁口深度过深,下次铁口难开,不仅严重浪费炮泥,而且加大设备维护工作量。
2. 改进措施及实施效果
2.1 改进措施
2.1.1 打泥液压缸控制回路改进
图2为打泥液压控制回路改进前、后对比示意图,图内P为高压油,T为回油,A为液压缸无杆腔,B为液压缸有杆腔,a为电磁阀左电磁铁,b为电磁阀右电磁铁,X为控制油口,Y为控制油回油口。
由图2(a)改进前示意图可见,电磁换向阀得电使双向液压锁打开,同时,比例阀电磁铁b得电,打泥液压缸活塞杆向外伸出,牵着钢丝绳经过滑轮组,带动指针旋转,指针转动角度的大小即为打泥量的多少[5]。从图中可以看出,液压泥炮的打泥活塞与打泥液压缸的活塞杆刚性连接,打泥液压缸活塞杆向外伸出的位移,即为液压泥炮泥塞走过的行程。据此,对打泥液压缸液压控制回路进行改进,将齿轮流量计串联在打泥液压缸的无杆腔油路上[6],同时,用编码器记录下齿轮流量计的转数输送给计算机,计算机按照设定的程序累加,把进入打泥液压缸无杆腔液压油的流量过滤、转换、处理,生成液压泥炮打泥量,通过数字显示仪显示出来,如图2(b)改进后示意图所示[7]。
2.1.2 打泥量计算公式推导
通过对液压泥炮在线使用工况条件及打泥量不准确的原因进行分析,找出解决问题的方案,根据流体力学“帕斯卡”原理[8],对打泥液压缸液压控制回路进行改造,改造后的示意图如图3所示。
图3中打泥液压缸移动的公共位移L,为液压泥炮打泥活塞的行程。通过介质?液压油流量进行理论计算,最终推导出打泥量计算公式[9]。
则有:
|
(1) |
由(1)得:
|
(2) |
|
(3) |
由式(2)~(3)得:
|
(4) |
式中:L为公共位移;Vn为液压泥炮打泥量;D为液压泥炮打泥活塞的直径(已知);d为打泥液压缸活塞的直径(已知);Vy为进入打泥液压缸无杆腔液压油的容积;Vc为齿轮流量计的齿轮几何容量(单转排量已知);η为齿轮流量计的转数。
由式(4)可知,由齿轮流量计的转数,就可以计算出液压泥炮打泥量。在液压泥炮向高炉铁口射炮泥过程中,编码器恰恰能够通过正弦波脉冲信号记录下齿轮流量计的转数,齿轮流量计每转一圈通过的流量即为齿轮流量计的齿轮几何容量(单转排量已知),即一个脉冲信号相当于一次齿轮几何容积的流量。脉冲信号转换为4~20 mA的模拟量信号传送给计算机,计算机接收4~20 mA的模拟量信号,按照设定的程序计算出液压泥炮打泥量,通过数字显示仪显示出来。
2.2 实施效果
2.2.1 堵铁口操作流程
图4为打泥量操作台及操作流程图,在使用时,每次堵铁口开始前,必须将数字显示仪上的数据清零。将操作台(如图4(a)所示)上的复位按钮按下去,待按钮自动弹出时,复位清零完成。堵铁口时,在操作室操作液压泥炮回转指令控制器手柄,进行堵铁口操作,在液压泥炮堵上出铁口的瞬间,再操作液压泥炮打泥指令控制器手柄,开始向出铁口射炮泥,数字显示仪开始动态显示打泥量(m3),当打泥量达到出铁口深度所需要的规定数值时,打泥指令控制器手柄复位,本次操作完成,打泥量清零及操作流程图(如图4(b)所示)。
2.2.2 改进后效果
本技术在高炉堵铁口操作中成功应用,能根据铁口的实际情况制定不同的打泥量,实现同一操作定量控制,不受人为经验判断因素的影响,维护了铁口的稳定性,为实现高炉稳产、高产提供坚实保障。避免了远距离观察和人为判断带来的较大偏差,通过计算机外部接口进行远程监控,实现自动化控制,每次打泥量的精度(实际用量减去理论用量的绝对值)控制在0.001 m3以内。本技术提高了炮泥的使用率,减少炮泥的使用量,不仅节约了炮泥费用,而且减少了高炉慢风损失,具有较大的经济效益。改造前,每年每座高炉炮泥平均采购费用1760万元,改造后,由于杜绝了操作原因、现场原因、特殊原因等诸多不利因素造成炮泥的严重浪费,每年每座高炉炮泥平均采购费用降低至1440万元,节省炮泥材料采购费用约320万元。
本技术解决了高炉出铁口打泥量过大导致铁口深度过深、下次铁口难开、浪费炮泥严重等现象,避免了高炉打泥量过少、铁口深度浅、出铁时间短或铁水放不干净等异常情况而严重影响高炉炉缸的寿命。液压炮打泥量累计总数复位到零,实现液压泥炮打泥量全程、时时、动态容积监控,从而达到精确控制打泥量。铁口合格率(铁口深度合格次数与总数的比率)由原来65%提高至98.5%。表2为打泥量装置改进前、后各指标对比表。
打泥量装置 | 打泥量精度/m3 | 炮泥费用/(万元/a) | 铁口合格率/% |
改进前钢绳式 | >0.076 | 1755 | 63.5 |
改进前重锤式 | >0.053 | 1765 | 61.5 |
改进前指针式 | >0.062 | 1760 | 65.0 |
改进后数字式 | ≤0.001 | 1440 | 98.5 |
3. 结束语
1)提高了炮泥的使用率,减少炮泥的使用量,具有较大的经济效益,每年每座高炉节省炮泥材料采购费用约320万元。
2)避免了远距离观察和人为判断带来的较大偏差,通过计算机外部接口进行远程监控,实现自动化控制,每次打泥量的误差控制在0.001 m3以内。
3)解决了高炉出铁口打泥量不准确问题,实现液压泥炮打泥量全程、时时、动态容积监控,从而达到精确控制打泥量。铁口合格率由原来65%提高至98.5%
来源--金属世界
来源--金属世界