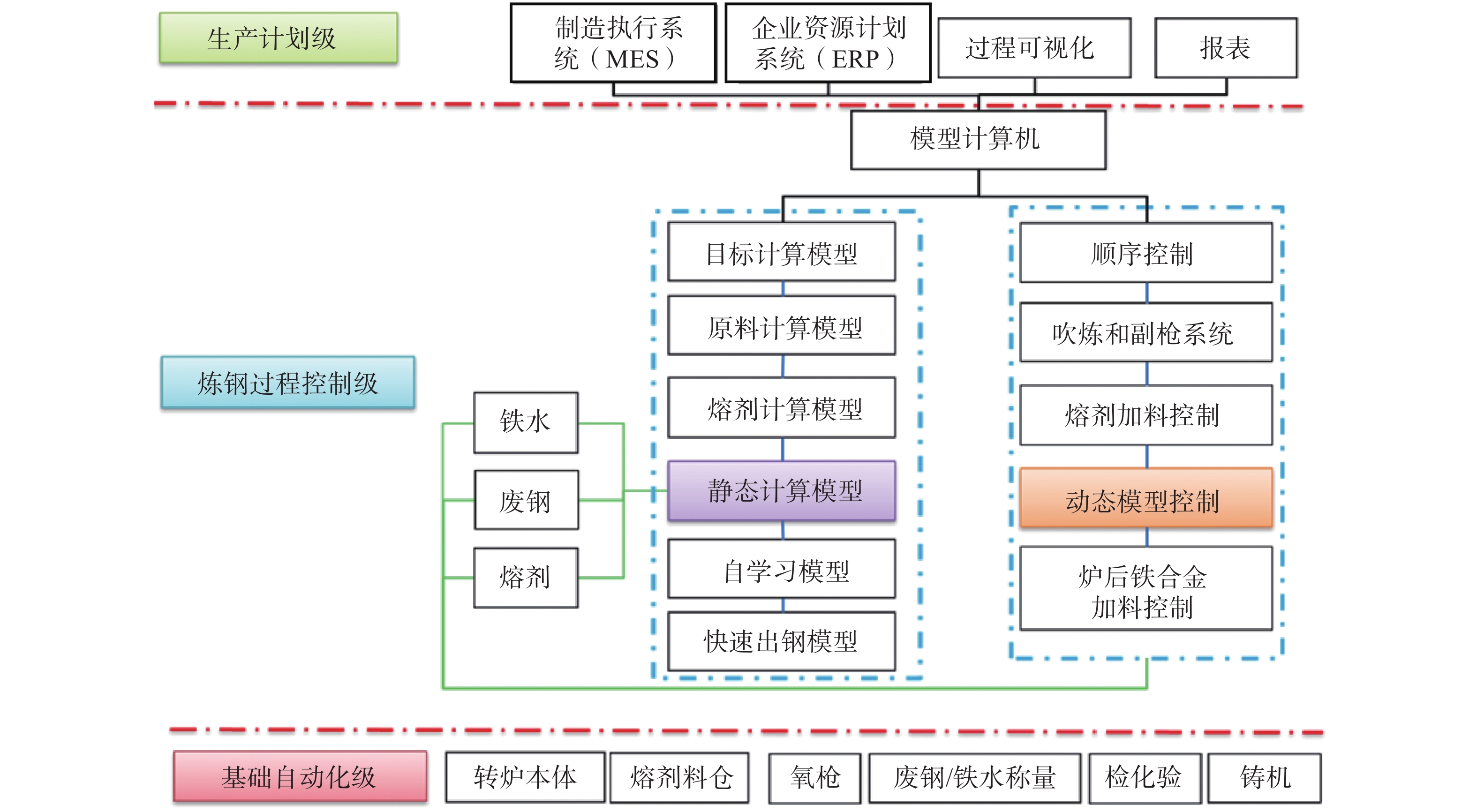
分享:转炉智能冶炼优化模型的研究与应用
工业大数据是工业生产过程中全生命周期的数据总和,是智能制造的核心,也是中国制造2025实施的关键支撑[1-4]。以“大数据+工业互联网”为基础,用云计算、大数据、物联网、人工智能等技术引领工业生产方式的变革,拉动工业经济的创新发展。对于钢铁行业来说,传统的大数据分析技术难以胜任高精度和高可靠性的要求,同时钢铁工业大数据也区别于离散生产的工业现场,需要建立基于工艺机理模型上的大数据系统,整合设备自动化、过程控制、生产控制、制造管理等数据,打通纵向和横向的数据孤岛,实现管控衔接和工序衔接,并利用数据分析结果反过来指导各个环节的控制与管理决策,并通过效果监测的反馈闭环,实现决策控制持续优化。
人们对钢铁的需求量与日俱增。但是传统的转炉炼钢技术存在着生产效率低下、耗能严重等问题,难以适应目前钢铁行业高速发展的需求,因此需要将传统的生产方式跟现代化的自动化控制技术相结合,提高转炉生产的自动化水平,使炼钢生产更智能化。
转炉炼钢自动化控制技术的应用,可以使复杂的转炉炼钢操作简单化,使转炉炼钢技术操作更加便捷,并且提高了钢铁产品质量,为钢铁企业带来了更多的经济效益和社会效益[5-6]。采用动态控制模型可实时了解转炉冶炼状态,达到高效冶炼的目的。因此将互联网工业大数据与自动化控制技术相结合起来,开发转炉冶炼模型,减少人工计算带来的误差,降低工人劳动强度,促进钢铁企业的转型发展是未来的发展方向[7-9]。
1. 转炉智能冶炼优化模型建立
转炉智能冶炼优化模型控制是在转炉动态控制的基础上采集控制模型、基础自动化、天车定位机自动识别及物流跟踪、数据采集与数据库管理等工艺设备数据,运用计算机建立的模型。
1.1 系统原理
转炉冶炼模型通过计算机系统采集控制基础自动化和炼钢过程计算机系统数据,进行实时通讯、存储、挖掘,用于计算机模型自学习自我完善。在转炉吹炼前,根据装入的铁水量、废钢量通过静态控制模型自动计算出各种辅原料的数量和加入批次,自动给出氧枪枪位曲线和氧气总量,并通过一级自动化发出指令自动调整氧枪高度和氧气流量,实时计算熔池脱碳速率。
利用音频曲线实时反映炉内渣料熔化情况,预测出熔池内能量与物料平衡及转炉熔池内熔渣与钢水成分温度变化情况,根据炉气分析等在线检测及时获得炉内信息,实时动态对转炉操作进行调整,实现吹炼过程全自动操作,终点碳、温度和终点P精确命中,计算合金加入量进行钢水成分调整,满足钢水浇铸成分要求,达到智能化自动化炼钢的目的。
1.2 系统架构
转炉冶炼模型系统是软硬件模型技术的综合体,由应用软件、标准化软件和设备服务器组成,主要组成简要描述(图1)。
转炉冶炼模型系统包括设备层、基础自动化(L1)、过程自动化(L2)和转炉冶炼模型四个子系统。设备层由现有的转炉及其配套机械设备和电气控制系统,包括转炉本体、加料、氧枪、底吹、检验分析及现场设备仪表。基础自动化(L1)包括转炉、加料、氧枪、底吹等可编程逻辑控制器(PLC)和计算机组成的控制系统,主要完成冶炼过程中数据和设备状况信息的收集,并根据模型指令完成设备控制过程的执行。过程自动化(L2)通过计算机和软件工程提高系统和操作过程的效率并降低操作工的劳动强度。
转炉冶炼模型通过烟气成分在线检测与现场数据采集,结合副枪系统,采用具有自学习功能的人工智能静动态控制模型,实时预测熔池内脱碳和温度变化,提高碳温命中率,降低生产成本,有效提高产品成分均匀性和质量的稳定性。在转炉主控室设置自动化炼钢操作站,计算机用于转炉冶炼模型监控及操作显示。
1.3 核心功能
转炉冶炼模型可根据磷的分配比计算石灰等辅料加入量,满足各种条件下的脱磷要求,比用碱度计算更合理,降低钢铁料消耗和石灰消耗;可对转炉终点碳氧积进行处理用于计算终点碳,具有自动排除异常和自适应功能;模型静态和动态都具有自学习功能,参数少且几乎不需要维护;操作画面少、简洁直观,可以通过数据传输全自动运行,同时便于操作工修改和输入数据;具有目标计算、枪位拟合、实时温度计算、烟气分析计算碳、渣况记录和预报、磷预测计算、锰预测计算等功能;具有模型使用效果和成本统计、评价、分析功能,可以取消现场人工记录和报表,投入少,接入灵活,不影响原有系统,可与原有模型并行处理。具体模型图如图2所示。
2. 系统功能设计
转炉炼钢模型在计算过程中首先要获得计算所需的模型参考炉次数据、钢种要求以及计算炉次装入数据和计算目标,然后计算石灰、镁球、助熔剂加入量、出钢量。通过模型静态自学习计算出当前炉次所需的矿石加入量、氧气量,按照加料、氧枪、副枪操作模式计算各操作步骤数据并计算合金。随后通过烟气分析实时计算熔池温度、碳含量、喷溅预测,动态实时计算熔池温度、碳含量。在冶炼结束获得当前炉次的实际加料量、吹氧量、停吹碳、停吹温度,并判断是否加入学习组,更新并保存自学习数据,同时动态参数自学习并更新数据子系统功能。
2.1 铁水采集子系统
铁水是智能炼钢系统的基础物料,因此对其装入质量、成分和温度数据采集十分关键,误差控制在0.5%内。通过过程数据采集,获得转炉工艺要求兑入铁水成分、温度、质量的信息通过网络送入智能化计算机系统,为转炉智能炼钢实时自动提供相关在线信息和数据管理。
2.2 废钢采集子系统
废钢的装入量及品质要求质量误差控制在0.5%内。废钢按照冶炼品种和工艺过程要求,天车工用磁盘吊吸入废钢的品种和质量,加到废钢斗中,计算机采集准确的入炉废钢的品种和质量。
2.3 转炉冶炼模型子系统
该系统是转炉冶炼模型的大脑和指挥中心。通过建立数学模型来对生产过程进行操作、优化和生成结果评估,从而不断提高系统稳定性和命中率。主要的数学模型有:主原料加料吹氧计算模型、主吹阶段控制模型、副吹阶段控制模型、底吹控制模型、钢水温度实时计算模型、副枪定碳模型、动态钢水碳和温度实时计算模型、合金料加入计算模型以及磷含量预测和快速出钢判断模型。
3. 模型系统运行效果
转炉冶炼模型系统作为管理、技术、操作相结合的平台,可提高终点控制精度和命中率,通过计算机控制炼钢终点命中率平均水平大于80%,先进水平可达到90%以上,与经验炼钢终点60%左右的命中率相比有大幅提高。模型具有先进的自学习功能,可精确计算吹炼参数,并不断优化,与经验炼钢的粗略计算相比更加精确,可自适应熔剂和废钢原料变化、转炉炉型变化,将其吹炼所需的氧气量和造渣剂用量控制在最佳范围。
采用基于智能型动态控制模型和低中高碳钢优化脱磷工艺模型,不受炉前操作人员水平状况影响,稳定生产过程得到碳、温度、磷成份均匀,波动范围小的合格钢水。运用系统可降低补吹率,静态控制炼钢再吹率一般情况下小于10%,而动态控制炼钢再吹率可控制到5%以下,比经验炼钢减少一半以上,同时系统具有快速出钢功能,模型炼钢时间比经验炼钢缩短2~10 min/炉,大大降低了钢水氧化性,提高钢水质量。
由于提高了钢水终点控制的精度和命中率,减少了倒炉补吹次数,从而降低终点炉渣氧化性(FeO降低1%~5%)和钢水氧含量(可降低30×10−6以上),大量减少在合金化和后处理中产生的夹杂物,从而提高钢水洁净度。采用转炉智能化自动炼钢技术可减少返吹次数,由此可防止钢水过氧化,并降低10%的钢水氧含量,降低炉渣中(FeO)含量1%~5%,更优化使用辅料和供氧。
根据炉气分析等在线数据,并结合转炉静态控制模型和动态控制模型,通过转炉基础自动化控制系统,实现对转炉的加料、吹氧、氧枪枪位、底吹搅拌、终点温度成分的全自动化控制和冶炼过程的实时监控和动态调节,实现一键式炼钢,使炼钢过程的操作实现规范化、标准化、科学化、智能化。同时,提供技术管理平台,有利于开展标准化作业,便于员工培训,减轻操作人员劳动强度,减少班组间技能差异,实现基础数据源惟一化,自动采集、存储炼钢重点过程参数,炼钢重点关键绩效指标(KPI)展示,自动生成炼钢日报表,提供炼钢过程数据惟一性,为大数据挖掘提供基础数据源。
通过评估钢水实际P含量以及温度的命中程度来评估转炉智能炼钢模型的实际运行效果。冶炼后的钢水P样本均值为0.020,有3%左右的样本超过上限值(0.035),过程基本可控。实际吹炼过程中,化验的钢水P比设定的目标P总体少0.006(样本均值−0.006),质量浪费现象较少。图3为钢水化验中P的分布情况,图4为钢水P偏差(化验-目标)的分布情况。
4. 结束语
本研究采用理论模型和数据修正结合的方法构建了转炉智能冶炼优化模型,有效的指导了转炉生产过程,克服了冶炼过程经验配料的不足,对降低冶炼成本和进一步智能化改造具有重要意义。本模型的优势在于:
(1)先进的自学习功能,冶炼结束获得当前炉次的实际加料量、吹氧量、停吹碳和停吹温度,判断是否加入学习组更新并保存学习数据进行动态参数自学习。
(2)提高了终点控制精度和命中率,经验炼钢终点命中率一般在60%左右,应用该模型计算机控制炼钢终点命中率一般水平大于80%,先进水平大于90%。提高了转炉冶炼的节奏,补吹率比经验炼钢降低一半以上,模型炼钢时间比经验炼钢缩短2~10 min/炉。
(3)实现全自动炼钢,降低生产成本,根据炉气分析等在线数据,并结合转炉静态控制模型和动态控制模型,通过转炉基础自动化控制系统,实现对转炉的加料、吹氧、氧枪枪位、底吹搅拌、终点温度成分的全自动化控制和冶炼过程的实时监控和动态调节,实现一键式炼钢。使炼钢过程的操作实现规范化、标准化、科学化和智能化。
来源--金属世界