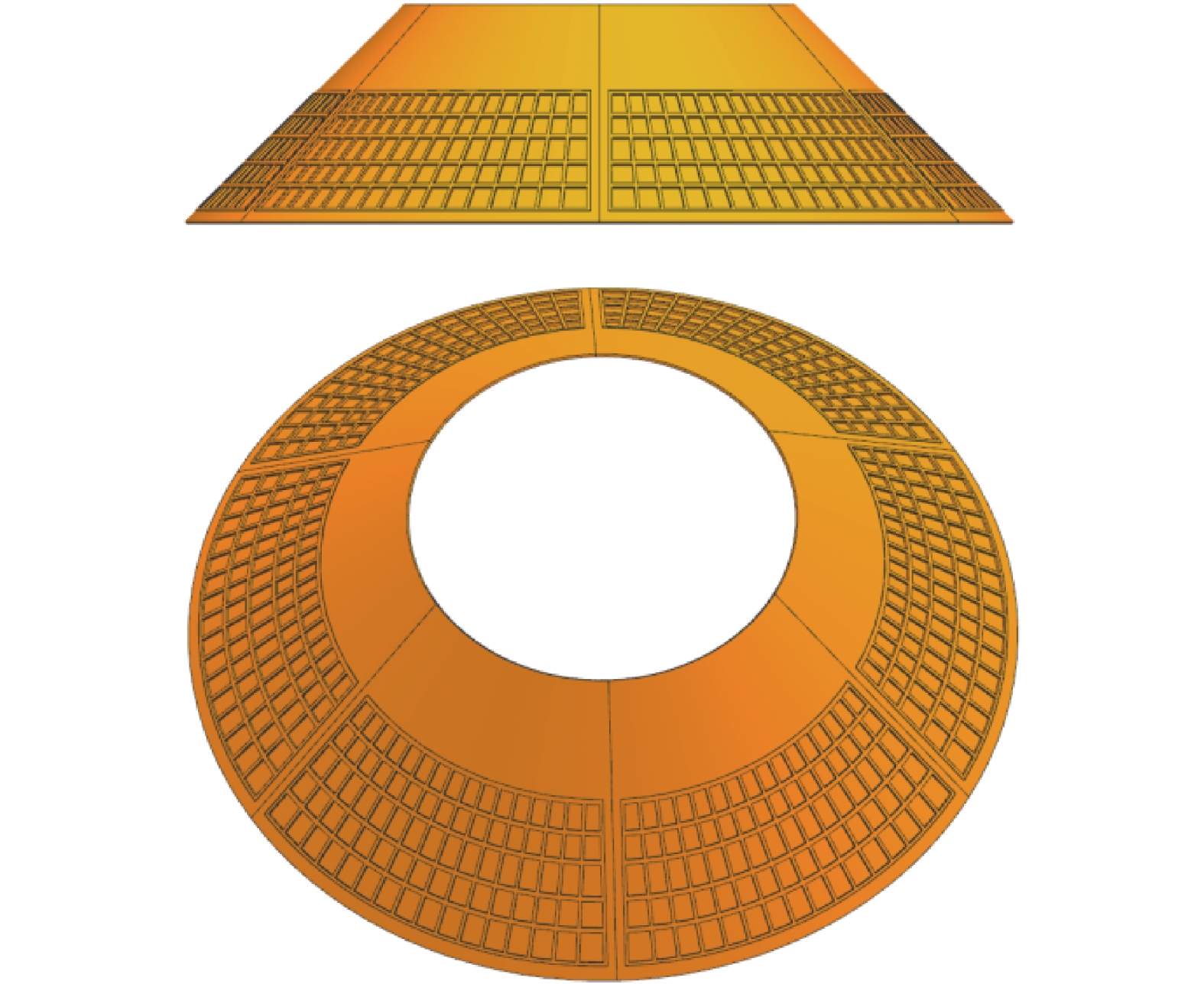
分享:一种大直径锥形零件的补偿铣削加工方法
随着航天制造技术的发展,航天产品结构日趋复杂,产品尺寸越来越大,加工精度要求也越来越高。由于锥形零件较球形零件和椭球形零件在空间节省方面更具优势,同时其力学性能更好,受力更加均匀,大直径锥形零件的应用越来越广泛。某大直径锥形零件属于典型的弱刚度薄壁件,同时产品铣削尺寸精度要求较高,在产品加工过程中,存在装夹困难、铣削基准找正困难等问题。本文通过研究大直径弱刚度锥形零件的补偿铣削工艺,设计装夹方案,寻找最优铣削参数,解决了该工件的加工难题。
1. 加工现状
1.1 产品结构分析
某锥形零件大端直径尺寸为4800 mm,小端直径尺寸为2200 mm,高度约1300 mm,整体壁厚仅有10 mm,如图1所示,属于典型的弱刚度薄壁产品。为满足搅拌摩擦焊较高的尺寸精度要求,在焊接前,需进行大端与小端的余量铣切工作,同时保证实际铣切边界与焊接理论铣切边界误差不大于0.1 mm,加工精度要求极高。
1.2 产品加工难点
1.2.1 装夹困难
零件尺寸较大,属于典型弱刚度零件,如无适宜装夹方案,加工过程中极易产生加工变形,无法保证铣削精度。
1.2.2 铣削基准找正困难
产品焊接要求尺寸精度极高,加工后实际铣切边界与理论铣切边界误差不大于0.1 mm。加工前,产品大端与小端已刻有理论铣切线,实际加工时,很难保证如此高的找正精度。
1.2.3 合理的铣断加工策略
为得到较高的铣削效率,减小加工过程中的震颤,需设计合理的铣断加工策略。
2. 加工方案
2.1 装夹方案
针对大尺寸锥形零件弱刚性的结构特点,设计适应锥形零件加工的装夹工艺。
2.1.1 回转中心的确定
为便于回转中心的确定,铣削夹具设计一圆形底座,铣削时的回转中心即为基座圆心位置,其余压紧装置及撑环均基于基座回转中心设计。
2.1.2 撑紧结构
为保证工装整体结构刚度,工装设计有横纵交错的加强撑杆。同时,在工装大端、小端设计有局部撑环,大端撑环、小端撑环的型面与零件内型面一致,已达到铣切区域局部接触支撑的目的。在撑环对应理论铣断区域设计有铣切槽,以保证刀具在铣断零件时的工装安全。
2.1.3 压紧机构
为实现产品的可靠定位,保证产品在加工过程中不发生移位,需设计合理的压紧机构。
在工装小端设计有均匀分布的6处压紧装置。压紧装置利用螺钉连接的形式固定于小端撑环上,同时利用螺杆连接的形式沿锥度母线方向手动向下施加压力,结合锥形零件接触面自锁特性,实现产品的可靠装夹。为避免螺钉突出带来的干涉问题,所有连接孔均设计为沉头孔的形式。为便于工装起吊,设计有4处工装起吊环。图2为锥底零件工装示意图。
2.2 产品铣断加工策略
为保证产品铣断对装夹可靠性的影响,优化工艺方案:产品吊装至铣切工装→调平→分段铣切大端余量→分段铣切小端余量→钳工连接处余量。
在产品切断时,当直接整周铣断时,易产生扎刀现象,造成刀具折断及产品铣伤,同时造成产品变形与装夹失效。优化铣切策略,采取6段均布铣断的方式,段与段间留10 mm连接余量,防止产品全部铣断时装夹失效的风险。最后,采用钳工将连接处余量锯断、打磨的方式保证产品精度,如图3所示。
产品铣断时,分粗、精加工。粗加工时,采用?10铣刀分层扎削的方式满吃刀去除余量,此时铣削工况较差,振动明显,留余量2 mm。产品自然时效24 h,充分释放产品内部应力,精加工时,在余量较小的情况下,利用铣刀侧刃去除余量,一刀到位,保证加工精度。
2.3 补偿加工策略
加工后实际铣切边界与理论铣切边界误差不大于0.1 mm,产品装夹调平时,很难保证如此高的找正精度。采用数据补偿的策略弥补调平误差。
产品调平精度控制在1 mm左右即可,精加工前,采用游标卡尺均布测量40个点的实际余量值,当相邻两点间余量变化范围介于0.3~0.5 mm时,两点间增加1个测量点,当相邻两点间余量变化范围介于0.5~1 mm时,两点间增加2个测量点,最终获得铣切边界分段后各段的余量分布情况,如图4所示。加工边界的实际位置曲线与加工边界的理论位置曲线对比,将余量误差补偿至铣加工程序,得到自适应加工路径[1]。采用补偿方案加工后的断面与理论铣切边界误差仅为0.05 mm,满足产品后续焊接需求。
2.4 切削参数优化
锥形零件产品粗加工时,刀具选择为小直径?10立铣刀,粗铣过程中,刀具的切削状态为全吃刀,切削状态不稳定,刀具磨损严重,同时由于锥形产品自身重力的影响,切断后,刀具承受沿母线方向的推力,极易造成刀具折断并铣伤产品,如图5所示。需通过在产品余量区进行切削实验寻找最优切削参数,改善刀具切削状态。
在薄壁件加工时,影响切削力、振动的因素主要是转速n、切宽ap、切深ae和进给量f,且切削参数对产品加工质量的影响因素的显著性依次为:切宽>切深>进给量[2]。综合考虑产品加工效率及产品表面质量,锥形零件粗加工正交实验的目标为获得小切深和适当每齿进给量fz的最优切削参数[3],见表1。
序号 | 转速n/(r/min) | 进给量f/(mm/min) | 切深ae/mm | 切宽ap/mm | 每齿吃刀量fz/mm | 表面粗糙度Ra/µm | 噪音等级 | 去除率/(cm3/min) | 备注 |
1 | 1500 | 300 | 1 | 10 | 0.05 | 1.6 | 1 | 9 | |
2 | 1500 | 500 | 3 | 10 | 0.08 | 3.2 | 2 | 45 | 推荐 |
3 | 1500 | 800 | 6 | 10 | 0.13 | 12.5 | 4 | 144 | |
4 | 2000 | 300 | 3 | 10 | 0.04 | 1.6 | 1 | 27 | |
5 | 2000 | 500 | 6 | 10 | 0.06 | 12.5 | 4 | 90 | |
6 | 2000 | 800 | 1 | 10 | 0.10 | 3.2 | 1 | 24 | |
7 | 2500 | 300 | 6 | 10 | 0.03 | 12.5 | 3 | 54 | |
8 | 2500 | 500 | 1 | 10 | 0.05 | 3.2 | 1 | 15 | |
9 | 2500 | 800 | 3 | 10 | 0.08 | 12.5 | 4 | 72 | |
注:噪音等级中1—几乎无;2—较小;3—一般;4—中等;5—严重。 |
兼顾加工效率,当切深选择为3 mm时,可以获得较高的表面加工质量,最优切削参数为n=1500 r/min,ap=3 mm,f=500 mm/min,fz=0.08 mm。采用最优切削参数进行锥形零件粗加工,未发生刀具折断现象,同时产品表面质量较好。
2.5 加工效果
本文通过研究大直径弱刚度锥形零件的补偿铣削工艺,设计装夹方案,寻找最优铣削参数等,实现了大直径弱刚度锥形零件的精密加工,加工后的断面与理论铣切边界误差仅为0.05 mm,满足了不大于0.1 mm的高精度要求。
3. 结束语
本文通过改进加工流程,设计可靠的装夹方式,同时采用补偿加工的方案,解决了大直径弱刚度锥形零件难装夹、不易找正的难题。采用局部仿形支撑的装夹方案既实现了产品可靠装夹,同时又降低了工装制造成本。通过补偿加工方案进一步提高了产品加工精度及加工效率。大直径弱刚度锥形零件的补偿铣削加工方案易于实现,实施效果明显,为同类型产品加工提供了加工经验。
来源--金属世界