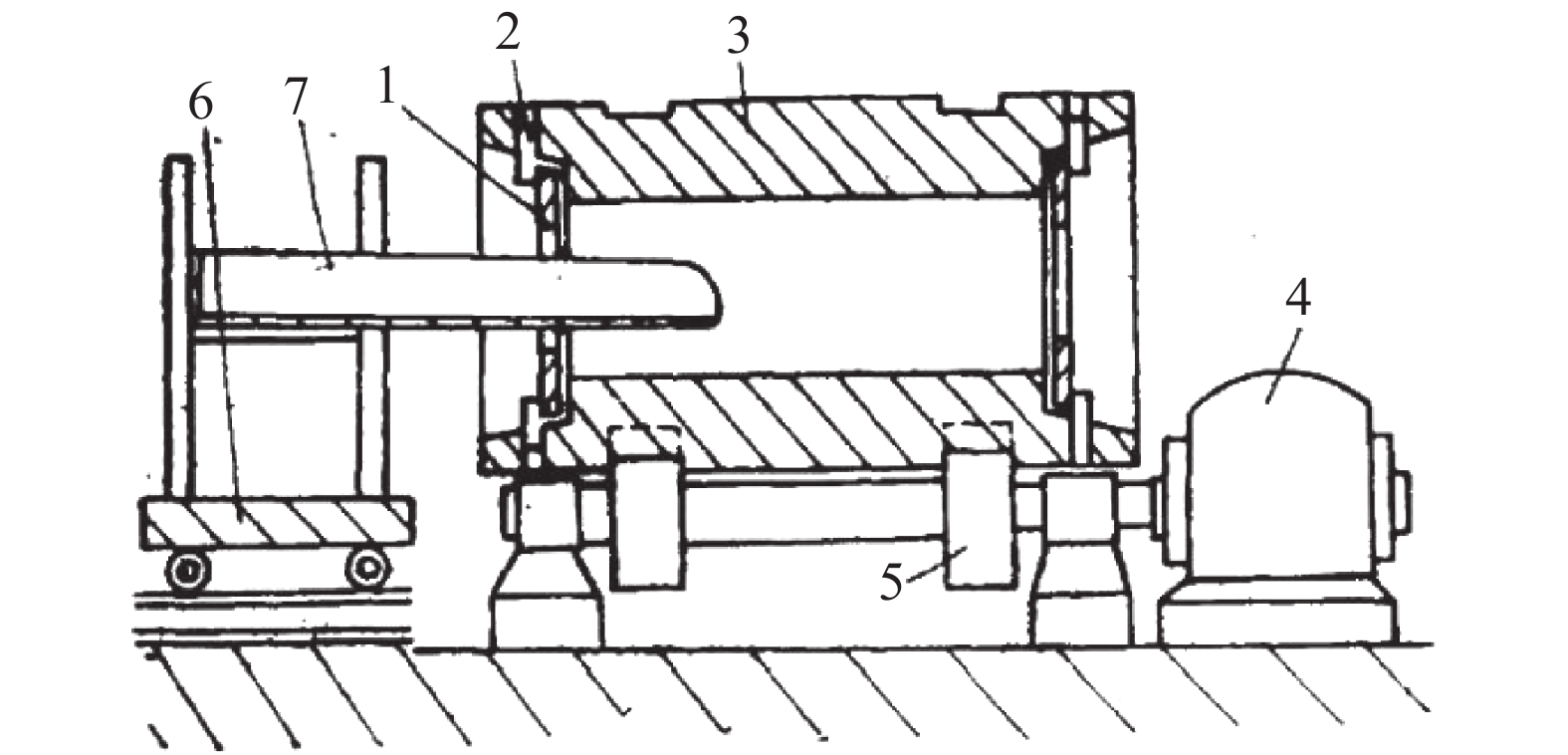
分享:离心喷涂方式在轧辊制造中的应用
离心铸造轧辊的金属型腔涂料挂涂工序主要采用滚挂涂料和手工喷涂两种操作方式。滚挂涂料方式是向滚动的金属型中倾倒涂料进行型腔覆盖,如图1。启动离心机旋转,涂料随溜槽进入加热过的金属型内腔,待型腔内气体排净后,涂料固化,停止旋转。手工喷涂方式顾名思义,即是操作人员持喷枪手动对加热过的金属型内腔进行喷涂作业。
上述两种方式的涂料层厚度控制困难,金属腔两端的涂料层薄厚不均,呈一定的轴线锥度,两端涂料厚度层差值>1 mm,这对轧辊辊身硬度均匀性及铸坯表面光洁度带来很大的负面影响。因此大量的轧辊生产厂家不断寻求新的金属型腔涂料挂涂工艺,其中邢台机械轧辊公司自主研发了自动喷涂料机设备。黄永渭等[1]利用离心喷涂方式制备的自动喷涂料机已成功解决了涂料层对轧辊辊身质量的影响。刘群山等[2]利用高速旋转的离心喷头,对预热过的金属铸型内腔进行涂料反复堆积来形成涂层,使得厚度均匀。因此,辽宁恒通冶金装备制造有限公司综合自动喷涂及离心金属铸型的优点,采用自动离心喷涂方式对金属型腔进行涂料覆盖,即在铸型旋转时将自动喷料枪伸入型腔内前后移动来进行圆面均匀喷涂作业,避免了滚挂方式或手工喷涂方式中涂料层厚度不均、排气缓慢、控制厚度困难等缺陷。综合离心喷涂方式具有涂料层厚度均匀、水气散发快、表面光洁度好和操作简便等特点。
1. 操作过程
1.1 材料及实验设备
离心喷涂选用磷酸铝涂料,其含有的偏磷酸铝Al(PO3)3胶结性强、悬浮性好,因此适合涂料的离心喷涂作业。首先选用200目高铝粉作为耐火骨料(化学成分见表1),磷酸(分析纯)与氢氧化铝粉混合作为粘结剂,水作为溶剂配制磷酸铝涂料[3]。其中氢氧化铝粉、磷酸、水按表2中要求的比例配制好,并加热至沸腾15~19 min,后将相应配比的高铝粉与之混合,倒入喷涂机料罐中不断搅拌18 h待用,设计涂料比重在1.4~1.9(使用波美比重计测量)。
SiO2 | Al2O3 | Fe2O3 | CaO | MgO | TiO | K2O | NaO |
5.57 | 87.93 | 2.17 | 0.22 | 0.13 | 3.87 | 0.1 | 0.04 |
高铝粉 | 氢氧化铝粉 | 磷酸 | 水 |
44 | 0.6 | 4.4 | 51 |
离心喷涂用金属型示意图如图2所示,尺寸规格为型腔直径×型腔长度,此金属型对应辊身规格为?600 mm×2400 mm的轧辊。为满足轧辊浇铸需要,设计金属型内腔喷涂料层厚度为3.0 mm,需涂料约60 kg。
1.2 离心喷涂作业
离心喷涂作业前需将图2中金属型预热至220~300 ℃,且要求金属型外表面与型腔内壁温度差≤10 ℃、型腔两端温度差≤5 ℃。自动喷涂料机及金属型转速按表3进行参数设置。
移动速度/ (mm/s) |
喷涂压力/ MPa |
喷吹次数 |
行程/ mm |
金属型转速/ (r/min) |
116.5 | 0.55 | 245 | 2599 | 150~210 |
将金属型放置在离心机托轮上,启动离心机,待达到要求转速后开启自动喷涂料机,喷涂料车的喷枪在金属型腔内进行前后往复式喷涂作业,如图3(a)中粗箭头指示方向。喷涂过程中注意观察喷枪是否有堵塞、涂料滴落现象,一旦发现立即刮除,中间不用停止作业。待涂料全部喷完后,停止自动喷料机及离心机,并检查喷涂料层表面(图4),仔细察看是否有涂料堆积、起皮、鼓包等缺陷。
1.3 喷涂料层厚度检测
喷涂完毕后,在型腔内涂料层轴向选择四条间隔90°的母线,每条母线用工具钻出等间距的?1 mm孔洞5处(深至金属型腔壁),并使用游标卡尺的深度尺进行涂料层厚度测量,数据见表4。
轴线 | 被测涂料点(孔洞)厚度/mm | ||||
1 | 3.2 | 3.1 | 3.2 | 3.0 | 3.2 |
2 | 3.2 | 3.0 | 3.1 | 3.2 | 3.2 |
3 | 3.1 | 3.0 | 3.2 | 3.2 | 3.0 |
4 | 3.2 | 3.2 | 3.1 | 3.2 | 3.1 |
从表4中可以看出,金属型腔内均匀分散测量的20个涂料层厚度在3.0~3.2 mm之间,涂料层厚度最大差值为0.2 mm,平均厚度约3.14 mm。由此可知,涂料层厚度均匀性及最大厚度与涂料层设计厚度(3.0 mm)的差值≤0.2 mm。
1.4 离心喷涂后金属型的使用
离心喷涂金属型确认合格后,将其运回燃气炉进行保温烘干,温度控制在200 ℃,并保温1~2 h。保温结束后的金属型即可用于轧辊辊身的铁水浇铸,轧辊辊身铁水成分如表5。
C | Si | Mn | P | S | Cr | Ni | Mo |
3.0~3.6 | 0.6~1.1 | 0.6~1.1 | ≤0.1 | ≤0.1 | 1.2~2.0 | 4.1~4.7 | 0.2~0.8 |
将保温烘干结束的金属型吊运至离心机托轮上,启动离心机转动,浇入铁水,浇注参数如表6。待铁水完全凝固后停止离心机,继续下一步轧辊铸型合箱、浇注轧辊辊颈铁水等工序,最后进行轧辊铸坯箱内保温。
金属型转速/ (r/min) |
浇注温度/ ℃ |
金属型转动 时长/min |
铁水量/ kg |
浇注速度/ min |
640 | 1370 | 28 | 2800 | 1.5 |
2. 实验结果与分析
2.1 实验结果
工艺要求辊身直径为?600 mm的轧辊铸坯在保温100 h后方可铸型开箱。轧辊辊身金属型开箱后观察铸坯表面质量。图5(a)为轧辊铸坯整体图片,图5(b)为铸坯辊身表面近景图片,从图中可以看出表面致密,且无粘铁情况。轧辊铸坯确认无缺陷后进行辊身车削加工,直径方向加工去除10 mm后进行肖氏硬度检测及超声波探伤,数据如表7。硬度检测是在辊身轴向选择间隔90°的4条母线,每条母线检测均匀间隔5点的硬度;轧辊辊身超声波探伤检测执行GB/T1504—2008标准。
由表7可以看出,此轧辊辊坯硬度范围在77.9~81.4 HSD,平均硬度为79.43 HSD,硬度均匀性为3.5 HSD。同时按照铸铁轧辊国家标准(GB/T1504—2008)中超声波探伤检测的要求,未发现铸造缺陷。
轴向 | 肖氏硬度HSD | ||||
1 | 79.5 | 78.7 | 80.2 | 78.8 | 78.7 |
2 | 80.4 | 78.7 | 80.7 | 79.9 | 77.9 |
3 | 77.9 | 79.0 | 80.8 | 81.4 | 79.6 |
4 | 78.2 | 80.4 | 77.9 | 80.3 | 79.5 |
实验中制造的轧辊是为某大型钢厂CSP轧机提供的?600 mm×2400 mm型热轧工作辊,技术标准要求辊身硬度范围为75~80 HSD、硬度均匀性≤5 HSD、探伤无缺陷,表明实验辊辊身各项检测项目均符合客户的技术标准要求。
2.2 理论分析
离心喷涂料方式覆盖金属型腔的优点可以从涂料层形成过程来分析,但无论是滚挂涂料方式还是离心喷涂料方式,涂料层均会形成粘结区、聚水层区和表层区3个厚度区域,如图6所示。两种涂料的喷挂方式在3个厚度区域形成的时间段上有所差异,主要以滚挂方式与离心喷涂方式对磷酸铝涂料层形成过程做分析。
2.2.1 滚挂方式
如图1中所示,滚挂方式是一次性将涂料液全部倾入滚动的金属型腔内,因此三个区域几乎同时形成。操作所使用的磷酸与氢氧化铝混合粘结剂在配制过程中的基本反应公式:
|
由公式知,磷酸铝涂料含有大量的磷酸二氢铝(Al(H2PO4)3)及反应水分,当涂料进入200 ℃以上的金属型内腔时,直接接触型腔内壁的涂料中的磷酸二氢铝与高铝粉迅速受热反应,固化形成粘结区,同时大量的水分受热向型腔中心的涂料层迁移;涂料层最内侧的表层区域也同时向型腔中心逸出水汽,并反应固化,因此在涂料层粘结区与表层区之间就存在着具有一定厚度并含有大量水分的聚水层区。
滚挂方式是在涂料倾入金属型前,在金属型两端先安装好端盖(如图1),以防止涂料液外溢,因此在涂料倾入金属型后,离涂料溜槽远端的涂料液受到金属型端盖的阻碍,形成回流,在此处的涂料层较另一端端盖处涂料层厚。金属型腔内部的蒸发水汽也同样受到金属型端盖的阻挡,并在金属型旋转的带动下形成涡流,难以排出。随着金属型的旋转,涂料层中的热量逐渐散失,聚水层区水汽迁移更加困难,造成金属型腔涂料覆盖工序作业时间延长。由于水汽的逸出困难,时而在涂料层表面上可观察到涂料起泡、鼓包的现象存在,同时后续金属型在燃气炉保温烘干中水汽仍在不断逸出,耗时耗能。
2.2.2 离心喷涂方式
如图3所示,离心喷涂方式是利用自动喷涂料车将喷枪伸入滚动的金属型内腔中,沿着金属型轴向中心线进行前后往复移动喷涂的操作过程,且金属型两端无需安装端盖,因此型腔内水汽较滚挂方式散发迅速。由于离心喷涂方式是以一定的压力将涂料液在金属型内腔壁上层层堆积,因此涂料层中的3个区域也分为先后3个阶段形成。
(1)最先形成的涂料粘结区:开始离心喷涂前期,涂料直接与金属型内腔壁接触,由于内壁温度高,涂料层中水分迅速从金属型两端散失,由于此时涂料层较薄,金属型的热量也能向涂料层传导更充分,所以此厚度区域内磷酸二氢铝与高铝粉骨料的受热反应也更容易进行,紧紧的粘覆在粗糙的金属内壁(Ra12.5)上,在涂料层3个区域中成型结合强度也是最高。
(2)涂料聚水层区:随着涂料在粘结区之上的层层覆盖、金属型旋转时间的延长,涂料层的温度也随厚度的增加而逐层下降,因此涂料层的水分散失、迁移也相对粘结区困难,水分含量的增加意味着涂料成型结合强度的下降,如果喷涂料车往复移动速度过快,致使涂料层堆叠速度增加,就会导致水分快速在涂料层内积累,因此离心喷涂过程中涂料的剥落、分层等问题也多发生于此厚度区域内。因而在离心喷涂中要控制好自动喷涂料车的移动速度,同时在喷涂后期配合提升50~80 r/min的小幅度金属型转速可使涂料层致密性更好。
(3)涂料表层区:喷涂料操作结束阶段,涂料层表层直接与空气接触,随着金属型腔内水汽全部散失殆尽,涂料层内外湿度梯度变大,水汽迅速从涂料层表面向外迁移,表面干燥程度高,因此涂料层表层光洁度较好、成型结合强度高。由于铁水浇入金属型腔后直接与涂料层表层接触,所以涂料层表层区的光洁度及其成型结合强度直接影响着轧辊铸坯辊身的成型质量,由表4知,离心喷涂方式涂料厚度均匀性非常高,均匀性≤0.2 mm,并且随着涂料层厚度均匀性的提高,由表7可以看出辊身硬度均匀性也达到了3.5HSD,较客户要求的辊身硬度均匀性(≤5HSD)降低了1.5HSD。
综上所述,由于离心喷涂操作方式使磷酸铝涂料层内3个厚度区域的水气排除更快、更彻底,因此涂料层的成型时间较滚挂方式更短,同时涂料结合强度也随之增加,整个涂料内外层整体质量大幅提升。
3. 结束语
离心喷涂料方式是利用自动喷涂料机层层喷涂金属型内腔,因此涂料层厚度均匀性得到极大保证,同时在自动喷涂料车移动速度设置合理的基础上,金属型腔中的水汽随着喷涂作业过程一同散失,涂料层中的水分得到快速的迁移、逸出,可大量缩短轧辊金属型腔涂料挂涂工序作业时长及金属型烘干时长。因而离心喷涂料的优势为:(1)较滚挂方式涂料层厚度均匀性更好;(2)较滚挂方式及手工喷涂方式操作更加自动化;(3)优化轧辊辊身硬度均匀性有着显著影响;(4)可大量缩短金属型涂料挂涂工序的作业时长,并间接节约大量能耗。
来源--金属世界