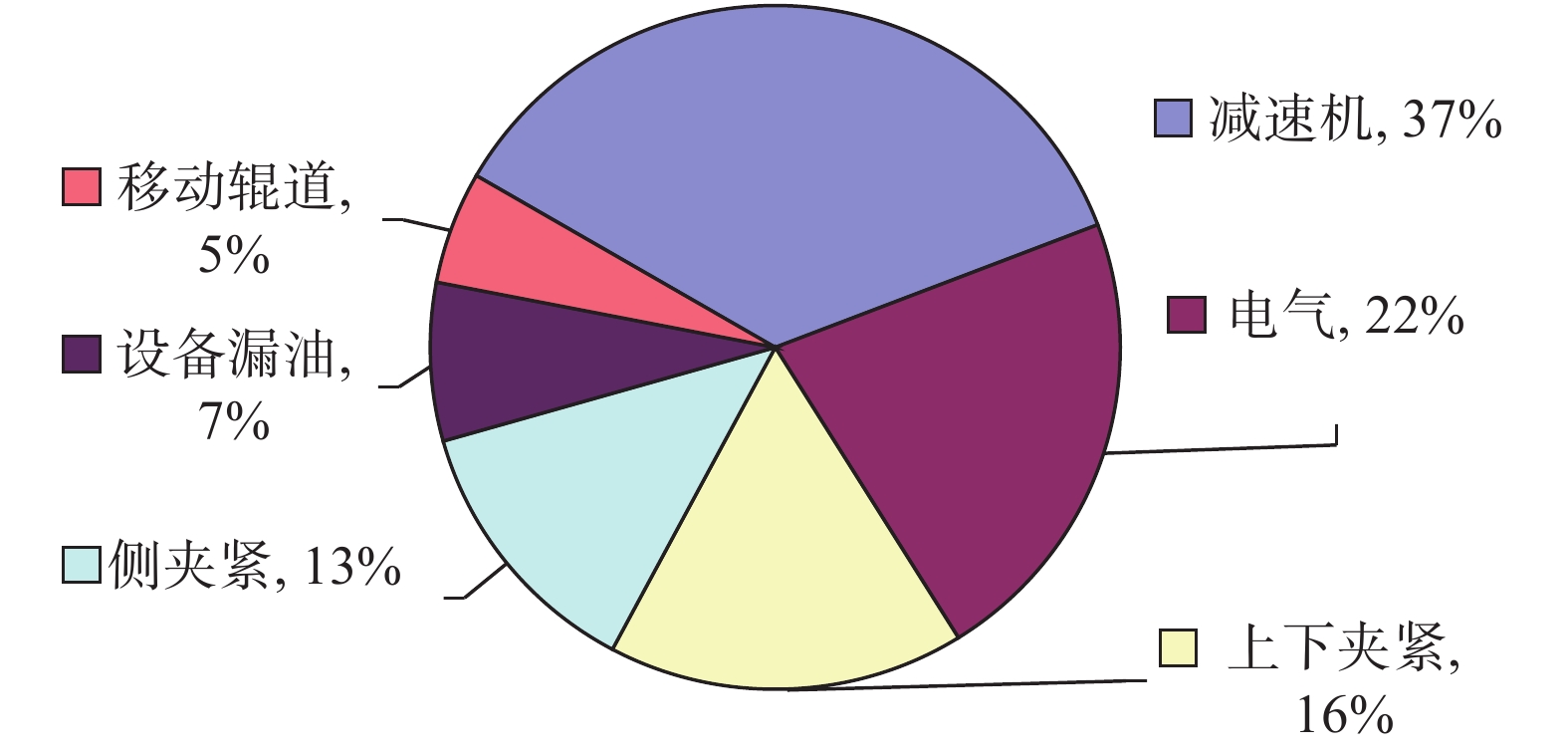
分享:小棒锯开动率的提高
本钢特钢厂轧钢车间小棒磨切锯组是整条轧线系统中最重要的部分之一。如果小棒磨切锯组在生产中出现故障,将严重影响正常生产,轻则打乱生产计划,重则会导致停机无法生产。而该套设备投产使用以来一直处于不良工作状态,给生产带来较大的损失。从过去5年小棒生产报表来看,小棒锯区的热停机占总热停机50%以上,严重影响小棒生产线产能的释放。
通过对故障频发点的分析,整体可分为:设备热停机——夹紧装置及减速机的损坏;生产热停机——锯片的损坏。针对以上问题,分别从设备设计缺陷及生产过程两个方面进行改进,保障生产顺利进行。
1. 小棒锯故障点分析
通过对2013年小棒锯故障热停机统计分析可知:设备热停机占78%,导致直接减产5000 t;生产热停机占22%,其中由于设备设计缺陷导致爆锯片占生产热停机75%。不难看出,设备是否完好、设计是否合理是生产能否顺利进行的重要保障,如果设备故障率得到有效控制,那么小棒生产线的产量将有质的飞跃。
设备热停机可以分为机械热停机和电气热停机(如图1所示)。由图1可见,机械热停机占78%,电气热停机占22%。减速机和夹紧装置热停机占总热停机66%,控制住这两项就可以大幅降低热停机时间。减速机故障主要是润滑方式问题,设备在初始设计中没有充分考虑到锯切工况的恶劣性。小棒锯夹紧装置故障频发主要集中在:生产?38~?50 mm棒材时侧夹紧液压缸脱离运行轨迹,缸头翘起使其弯曲变形从而无法正常使用;上夹紧升起不到位,棒材无法正常通过,撞坏夹紧装置。
生产热停机主要是爆锯片。爆锯片的原因可分为设备影响、锯片质量、安装操作三方面,其中设备影响主要是上下夹紧压力匹配不稳导致锯片在切断过程中发生爆裂。
综上所述,如果减速机及夹紧问题得以解决,那么小棒锯区的热停机必然会大幅下降。
2. 装置组成及原理
2.1 减速机
小棒锯减速机主要由4根传动轴、1组伞齿轮副、2组斜齿轮、润滑系统及箱体组成,主要完成传动比为1.3:1的增速运转。
2.2 夹紧装置
夹紧装置主要由夹紧装置框架、2对上夹紧(4个液压缸)、2对下夹紧(8个液压缸)、1对侧夹紧(2个液压缸)组成。夹紧装置驱动形式为液压驱动,使用SIEMENS PLC400控制系统。动作顺序为:根据订货商提供的棒材尺寸要求,通过液压马达动作将整个夹紧装置及小棒锯调整到合理的位置,锁紧液压缸锁紧后,小棒锯进入正常动作的等待状态,等钢棒到达预切长度时:辊道停止转动—下夹紧上升—上夹紧下降—侧夹紧推出,然后在等待位的小棒锯开始切钢,等切断钢后:侧夹紧收回—上夹紧上升—下夹紧降下,小棒锯退回等待位,完成一次动作。其中动作指令由接近开关及位移传感器控制。
3. 存在问题及改进措施
3.1 减速机
3.1.1 存在问题
(1)伞齿轮副损坏。轮齿折断:轮齿单侧工作时,根部弯曲应力一侧为拉伸,另一侧为压缩,轮齿脱离啮合后,弯曲力为零。因此,在载荷的多次重复作用下,弯曲应力超过弯曲持久极限时,齿根部分将产生疲劳裂纹。裂纹逐渐扩展最终引起断齿,或者轮齿因短时过载或冲击过载而引起突然折断。在2013年生产过程中发生了2次轮齿折断,1次齿与齿啮合不上。
(2)减速机轴承及润滑故障。2013年减速机轴承损坏5次。轴承损坏原因主要为:轴承温度过高和轴承噪音。轴承温度过高:润滑油质不符合要求或变质;润滑油黏度过高;机构装配过紧(间隙不足);轴承装配过紧;轴承座圈在轴上或壳内转动;负荷过大;轴承保持架或滚动体碎裂等。轴承噪音:滚动轴承在工作中允许有轻微的运转响声,如果响声过大或有不正常的噪音或撞击声,则表明轴承有故障。2013年润滑系统齿轮泵损坏3次。
3.1.2 改进措施
伞齿轮副损坏主要是传动轴窜动所致,如果能在轴向窜动初期及时发现将能避免类似事故的发生。防止伞齿轮窜动的机构只有前端挡盖。为防止传动轴发生窜动,在原设计的基础上,将所有固定螺栓用细钢丝连接在一起,从而防止螺栓松动。只要钢丝断裂就可以直观发现传动轴产生窜动并及时进行处理。伞齿轮前端挡盖采用同样的方法,有效避免了类似事故再次发生。
减速机轴承及润滑故障出现的主要原因是轴承润滑不到位。润滑油管在铺设及润滑点的选择上,原设计只考虑到了理论上存在的问题而忽略了设备现场的工作情况,磨切锯在工作过程中产生大量的铁屑和含胶粉末等混合粉尘,这些粉尘极易通过润滑系统的循环过程堵塞供油孔,并且这些供油孔在生产停机过程中无法进行疏通检查。根据现场实际情况对供油孔进行改进,方便定期疏通检查,如图2所示。
3.2 侧夹紧装置
3.2.1 存在问题
(1)液压缸活塞杆弯曲变形。出现弯曲变形的主要原因是侧夹紧液压缸活塞设计直径为?56 mm行程为1500 mm,当活塞杆接近满行程时,活塞杆受到轻微的外力冲击就会出现弯曲变形。当锯切?38~?50 mm棒材时由于活塞杆行程过长导致液压缸活塞杆容易偏离轨迹跑到棒材上方。这样不仅无法满足生产使用要求,也降低备件的使用寿命。
(2)爆锯片及锯渣对液压缸的影响。当锯切?38~?50 mm棒材时需要侧夹紧液压缸持续推动才能满足生产要求。但是,由于锯片质量及钢材硬度等综合因素会导致锯片爆裂,当爆裂锯片落到活塞杆上时,会划坏活塞杆表面,被划坏的活塞杆在下次工作过程中会损坏缸体内密封圈,导致液压缸漏油。
当磨切锯连续切削时间超过8 h后,下夹紧上表面的锯渣高度超过3 mm。这样侧夹紧液压缸在频繁动作时会使下夹紧工作表面出现斜面。当斜面的倾斜角过大或斜面高度大于5 mm时,侧夹紧液压缸在工作时就会偏离轨道发生弯曲变形(如图3所示)。
3.2.2 改进措施
针对液压缸活塞杆弯曲变形问题,更改液压缸,将活塞杆的直径从原来的?56 mm更换为?100 mm,提高活塞杆的抗弯强度5倍以上。根据现场的实际工作环境,将原行程为1500 mm的活塞杆更换为1120 mm(如图4所示)。
为了降低爆锯片对活塞杆的损坏并且满足生产要求,将侧夹紧液压缸从夹紧框架里分离出去,变成一个独立的个体。将液压缸横移到减速机的前端,用减速机作为掩体能有效对液压缸进行保护。由于侧夹紧液压缸从夹紧装置里分离出来,因此就没有了下夹紧上表面积渣平台的影响,但是有必要加大原设计的夹紧碰头,防止侧夹紧液压缸在工作时偏离轨道发生弯曲变形。
3.3 上下夹紧装置
3.3.1 存在问题
(1)上下夹紧控制压力匹配不均衡。在设计上,要求下夹紧的工作压力大于上夹紧的工作压力,保证锯片在切削过程中不会被棒材夹住。但是,在实际操作过程中,由于阀台压力波动及锯渣卡堵等综合因素影响,根本无法达到设计要求,经常出现棒材夹住锯片导致锯片爆裂的现象。
(2)锯渣的清理问题。下夹紧在升起后锯片与夹紧装置之间的距离只有30 mm,这样小的距离很容易引起锯渣的堆积,影响锯片的使用寿命。
3.3.2 改进措施
上下夹紧控制压力匹配不均衡的改进措施:根据原设计理念,锯片在切削过程中依靠压力差来保证切削过程中切断口处始终存在向外的拉力。为了达到这种设计理念,可以通过杠杆原理来实现。将现有的上夹紧向辊道外平行移动100 mm,上夹紧压钢的力通过将辊道作为支点,将力作用在切削口处,不仅能达到设计目的,而且向外的拉力作用稳定。
锯渣的清理问题改进措施:上夹紧分别向辊道外移动100 mm后,达到设备设计功能的同时,就能将下夹紧拆除,释放出有限的空间来,方便操作工清渣和维护人员检修,如图5所示。
4. 结束语
通过对锯切设备工作原理的分析,找出影响锯切正常工作的原因,拟定改进措施:(1)加固减速机传动轴及改进润滑方式,延长减速机的使用寿命;(2)改进液压缸,提高活塞杆的抗弯强度;(3)改变液压缸的位置,降低爆锯片及锯渣对锯片的影响。改进措施的实施取得了良好的效果,提高了锯切的工作效率,同时提高了备件的使用寿命,降低了备件费用。
来源--金属世界